Разгон и модификации
Подписаться на эту рубрику по RSS
Введение
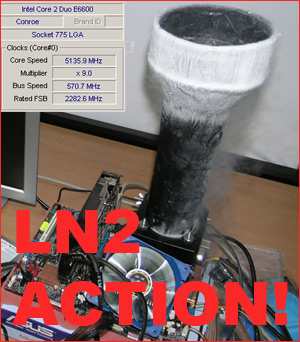
Первый раз мы писали про экстремальный оверклокинг в 2003 году, когда получили в распоряжение систему фазового перехода Asetek VapoChill XE. Совместные усилия Тестовой лаборатории ITC и руководителей сообщества энтузиастов ModLabs.net вылились в весьма впечатляющие достижения по «выжиманию» производительности из ПК.
Эта статья является расширенной версией материала, опубликованного в июньском номере журнала «Домашний ПК» за 2007 год. Отчёт дополнен значительно более подробным описанием процесса подготовки к бенчмаркингу с использованием жидкого азота – для тех, кто желает повторить наши эксперименты.
Ориентируясь на главный рейтинг мастерства оверклокеров – Futuremark O.R.B., мы вначале поднялись в нем в ТОР-20 абсолютного зачета, а затем, используя только что вышедший на тот момент процессор Intel Pentium 4 Extreme Edition 3,2 GHz, дошли до третьей позиции! Для того, чтобы достичь подобного, мы выжали максимум из всех ключевых компонентов: серьезные модификации были внесены в конструкцию материнской платы и видеокарты, использовалась самая производительная на тот момент оперативная память на легендарных чипах Winbond BH-5...
С тех пор мы неоднократно возвращались к теме разгона процессоров с помощью «фреонок» ECT Prometeia 2 GT и Asetek VapoChill LS, да и руководств по вольтмоддингу различных компонентов было написано немало, но и то, и другое уже давно перестало быть действительно экстремальным оверклокингом.
Появление HwBot.org создало новую мотивацию для многих оверклокеров для того, чтобы вернуться к активному бенчмаркингу. Вот и автор этой статьи решил «тряхнуть стариной» и наконец-то воплотить в жизнь давнее желание поэкспериментировать с охлаждением жидким азотом, чтобы помочь своей бенчмаркинг-команде Team MXS ModLabs.net в борьбе за место в мировом ТОР-3.
Бенчмаркинг-сцена 2007
Прежде чем рассказывать собственно о наших экспериментах, стоит вкратце описать ситуацию на бенчмаркинг-сцене на данный момент, так как именно это стало причиной для нашей активизации на этом поприще.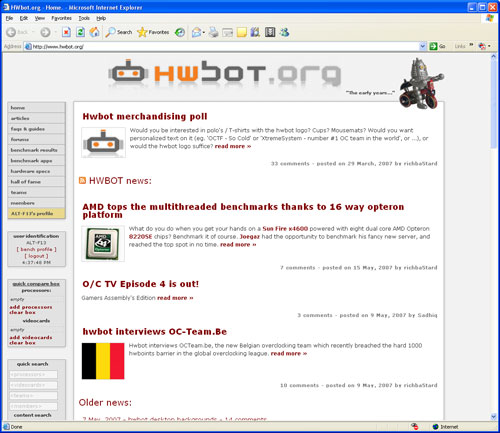
В прошлом году произошло важное событие в мировом сообществе оверклокеров, значительно изменившее суть непрерывного соревнования экстремалов. Традиционно рекорды фиксировались в тестовых пакетах производства Futuremark и в качестве главного рейтинга достижений много лет служил O.R.B. Кроме того, отдельные списки рекордсменов велись и ведутся неофициально по SuperPi, PiFast и тактовой частоте CPU. Не хватало некоего механизма интегральной оценки мастерства оверклокеров и, что еще более важно, рейтинга командных достижений сообществ. Такой рейтинг создал бельгиец Фредерик «richba5tard» Колардин (Frederik Colardyn) и располагается он по адресу www.hwbot.org. Суть проекта: кроме удобных рейтингов производительности ПК в 13 тестовых приложениях (все продукты Futuremark, а также Aquamark 3, SuperPi, PiFast, wPrime и CPU-Z) участникам начисляются баллы за выдающиеся результаты, что позволило организовать «общий зачет».
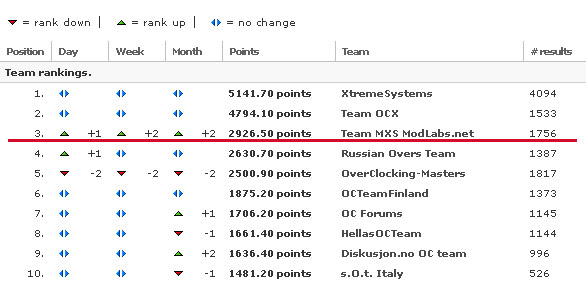
На сегодняшний день в рейтинге участвуют более 300 команд, состоящих из 5500 членов – как весь цвет оверклокерского сообщества, так и небольшие малоизвестные коллективы. Команда Team MXS ModLabs.net, являясь старейшим и крупнейшим объединением оверклокеров в СНГ, достойно выступает в HwBot. На данный момент мы заметно уступаем только двум признанным мировым лидерам – командам XtremeSystems и Team OCX. Дружеская конкуренция с другой русскоязычной командой, Russian Overs Team, на протяжении нескольких месяцев заставляет нас не сбавлять темпов бенчинга: с января и мы, и R.O.T. поднялись с середины второго десятка командного рейтинга почти до вершины, втрое увеличив количество своих очков. Текущие позиции двух наших команд - третье-четвертое место, на которых мы регулярно меняемся местами, но, разумеется, стремимся догнать и перегнать двух лидеров.
Подготовительные работы
Организация охлаждения с помощью жидкого азота, на самом деле, весьма несложная вещь – скажем, сборка самодельной системы фазового перехода на порядок сложнее. Более того, по материальным затратам эксперименты с жидким азотом (или сухим льдом – технология та же самая) тоже заметно более демократичны. Готовясь к бенчинг-сессии, необходимо выполнить несколько действий. Описывая их в журнале, мы ограничились кратким перечислением. Теперь же рассмотрим все аспекты в подробностях. Возможно, некоторые пункты покажутся даже избыточно подробно расписанными – что ж, в таком случае мы рады вашей проницательности и предусмотрительности. Ниже описывается наш собственный опыт и, несмотря на то, что организацией азотной сессии занимались несколько человек с многолетним стажем оверклокинга и бенчмаркинга, мы неоднократно обнаруживали себя в достаточно глупых (если смотреть на них «опосля») ситуациях.Disclaimer
Внимание: жидкий азот – сильнотекучее вещество с температурой -196 С, что означает его высокую опасность для жизни и здоровья при неправильном обращении. Автор статьи и ModLabs.net не несут НИКАКОЙ ответственности за любой ущерб имуществу или здоровью, нанесенный вследствие повторения действий, описанных в данном руководстве.1. Стакан
Во-первых, необходимо изготовить так называемый «стакан» - сосуд с металлическими (медными или алюминиевыми) дном и стенками, который устанавливается непосредственно на процессор. Стоимость его производства, в зависимости от материалов и конструкции, колеблется от 50 до 300 долларов. Именно с создания или покупки стакана следует начинать подготовку к экстремальному оверклокингу.Разумеется, ни одна компания не производит подобные агрегаты серийно – объемы выпуска были бы слишком незначительны для того, чтобы экономически обосновать такую затею. Зато несколько энтузиастов предлагают результаты своих усилий в продаже через интернет (как правило, на специализированных оверклокерских форумах в разделе «Продажа»). Наиболее известным в мировом масштабе поставщиком стаканов является MickeyMouse, разработчик серии Mousepot. Его творения можно приобрести за сумму от 300 долларов и выше. У других поставщиков, как правило, цены гуманнее, но Mousepot уже стали «стандартом индустрии». На территории СНГ великолепной конструкцией стакана отличился небезызвестный ТаРаКаН из Эстонии, член команды Team OCX.
Основная проблема в разработке стакана – это обеспечение минимальной температуры процессора в полной нагрузке. В отличие от воды, жидкий азот не является хорошим проводником тепла, он всего лишь очень холодный, за счет чего промораживает стенки стакана. Так как тепловыделение процессоров в простое и в загрузке отличается очень существенно, а скачки происходят мгновенно, стакан не в состоянии эффективно отвести тепло: разница между температурой в этих двух режимах может достигать 60-70 градусов! Как следствие, частота стабильной работы даже таких коротких тестов, как Super PI, будет существенно отличаться от предельно возможной для снятия скриншота CPU-Z – так называемого suicide screen.
В целом, оптимальная конструкция, которая обеспечивает минимальные потери теплопередачи и наилучшие температуры в загрузке, похоже уже найдена. Ее принципиальную схему (в данном случае это Vikingpot производства ТаРаКаН’а) можно увидеть в этой статье. Для того, чтобы ее повторить, необходим достаточно большой цельный брусок меди и доступ к токарному станку. Главная проблема здесь именно в меди: стоимость такого количества из-за огромного веса превысит $100, причем большую часть придется просто выбросить в виде стружки. В качестве альтернативы, возможно использование алюминия – это позволит снизить и вес, и цену изделия, но итоговые характеристики окажутся несколько хуже. Тем не менее, многие оверклокеры используют именно алюминиевые стаканы и, в принципе, нельзя сказать, что они добиваются существенно худших результатов.
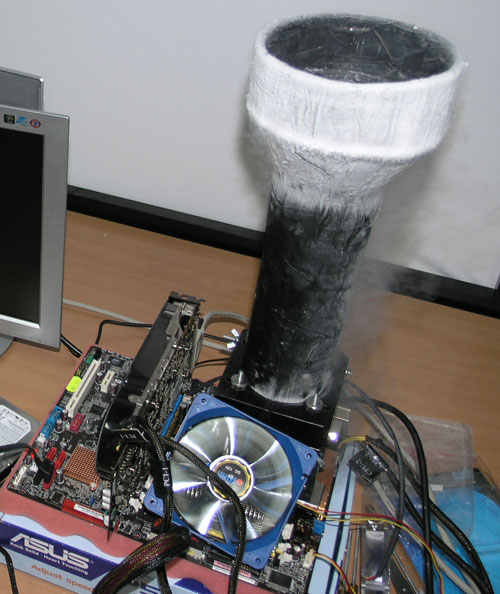
Честно говоря, тот стакан, который есть у нас – очень плохой. Конструкция дна была экспериментальной, принципиально отличающейся от рекомендованной лучшими «азотоводами» и изначально высокие результаты даже не ожидались. Но, как оказалось, на момент проведения теста это был единственный из доступных нам стакан, который был полностью готов. Но наш мастер на все руки VER-VOLF уже завершает создание более традиционных конструкций, что позволяет надеяться на улучшение результатов при следующих «подходах к снаряду».
Конструкция паянная: медное фрезерованное дно припаяно к медной же трубке диаметром 50 мм. Разумеется, далеко не каждый припой выдержит температуры жидкого азота. Как сказал VER-VOLF, этот стакан был сделан на припое ПОС 61 и, как видите, пока держится. По сравнению с цельноточеными стаканами стоимость такого изделия резко ниже, так как вместо пяти-семикилограммовой медной чушки надо купить всего лишь банальную трубу подходящего диаметра и небольшой брусок для дна. Но, как сказано выше, вместо доступа к токарному станку нужно найти фрезеровальный плюс хорошего сварщика.
Зато существенный плюс нашего стакана: большая высота, что позволяет залить много азота и не беспокоиться о постоянном доливании (хотя и ценой дальнейшего снижения эффективности) на протяжении как минимум десяти минут. Незаменимая вещь, если в организации сессии участвует только один человек, так как одновременно быть «кочегаром» и гонять тесты достаточно затруднительно. Также обратите внимание на воронкообразный верх – так значительно проще (как минимум психологически) заливать в стакан азот, не боясь пролить его на плату.
Итак, медный или алюминиевый стакан готов. Что дальше?
2. Теплоизоляция и крепление
Дальше нужно качественно теплоизолировать сам стакан и материнскую плату для того, чтобы конденсат, образующийся от огромного перепада температур, не замкнул какие-нибудь контакты на ней.Разновидностей теплоизоляции на рынке – море, можно выбрать тот, который наиболее удобен. Обычно для изоляции стакана рекомендуют трубки из пенистого материала, которые подбираются по диаметру и надеваются сверху. У нас трубок не было, зато был теплоизоляционный материал в листах. Кстати, отличные свойства имеет популярная шумоизоляция (!) akasa Pax-Mate.
Отрезав необходимый кусок, мы обмотали стакан в несколько слоев, покрыв его сверху черной изолентой для надежного крепления и придания хоть немного хорошего внешнего вида. Как оказалось, такой изоляции оказалось вполне достаточно – на протяжении первого часа-полутора конденсат вообще не появлялся на внешних стенках стакана, да и в дальнейшем его выпадение было весьма незначительно по сравнению с публикуемыми в Сети фотографиями насквозь промерзших конструкций.
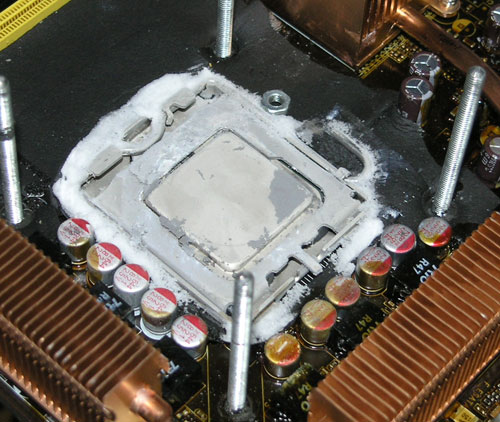
С материнской платой несколько сложнее. Дело в том, что в любом случае есть шанс, что конденсат где-нибудь выпадет и место это будет неудачным. Поэтому рекомендуется покрыть поверхность платы (включая силовые детали и бескорпусные элементы, но, конечно, исключая все разъемы – от процессорного сокета до SATA-портов!) диэлектрическим лаком. Разъемы при этом необходимо тщательно заклеить – естественно, в них лак как раз попасть не должен. Также следует покрыть обратную сторону платы в районе процессорного сокета. Смысл этой операции в том, чтобы попавшая на плату влага не смогла ничего закоротить даже в том случае, если окажется на ножках какого-нибудь контроллера. Можете считать данный совет излишней предосторожностью, но от случайностей никто не застрахован. Разумеется, покрытие платы лаком с большой вероятностью окажется заметным и, таким образом, лишит вас гарантии на нее. Вряд ли это сильно беспокоит, но мы считаем своим долгом вас об этом проинформировать.
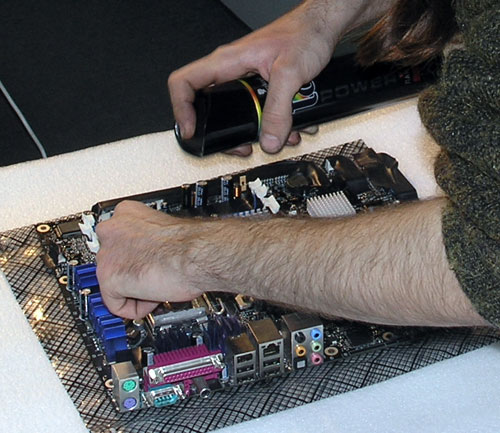
При первой операции такого рода на Intel D975XBX2 у нас случился конфуз. В порыве изоляционистского рвения покрыть лаком решили не только область возле сокета (т.е. там, где реально может выпасть конденсат), но всю плату в целом. Во-первых, лак оказался не совсем диэлектрическим. Во-вторых, возможно, мы недостаточно тщательно заклеили какой-то из разъемов – в итоге плата стартовать перестала. После купания в ацетоне плата заработала и, вновь покрытая полностью, но уже другим лаком, работает до сих пор. Кстати, так как плата работает длительное время в обычной системе, можно констатировать факт – само по себе покрытие лаком всех элементов платы не влияет на ее работоспособность. Зато теперь можно не опасаться протечки системы водяного охлаждения!
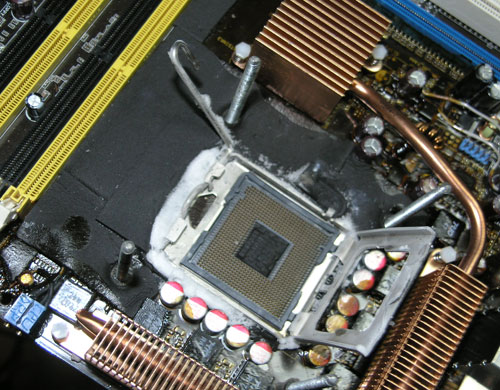
После лакировки платы приходит черед ее теплоизоляции. Во-первых, очень рекомендуется избавиться от воздуха в центре процессорного разъема. Мы использовали для этого seal string из комплекта системы фазового перехода ECT Prometeia 2 GT. Вместо этого можно просто положить туда квадрат из теплоизоляционного материала.
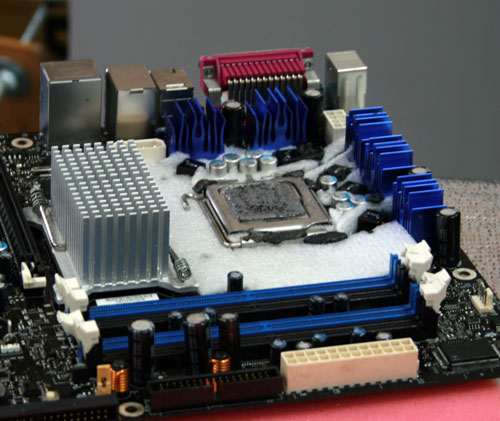
Во-вторых, необходимо изолировать все пространство вокруг сокета таким образом, что теплоизоляция стакана плотно прилегала по всему периметру к изоляции материнской платы, без доступа воздуха внутрь. По такому же принципу создания пространства без доступа воздуха извне сделаны механизмы теплоизоляции серийных «фреонок». Однако, у нас есть еще одна опасность: что конденсат в виде снега таки начнет намерзать на самом стакане или даже на самой материнской плате. Поэтому стоит изолировать также несколько большую часть платы, чем закрываемую стаканом. Но будьте очень внимательны: в отличие от лака, покрытие силовых элементов и микросхем теплоизоляцией недопустимо – без притока воздуха они могут перегреться и сгореть! Для их охлаждения следует вырезать отверстия в изоляции по размеру чипов.
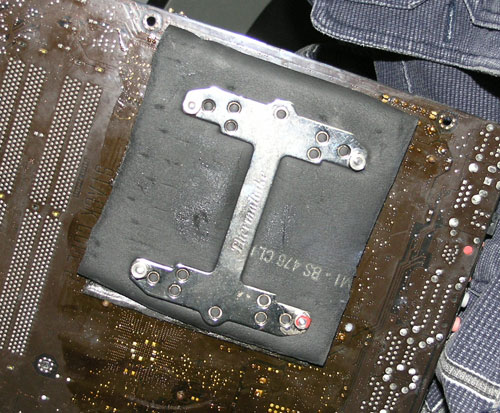
С обратной стороны платы, если на ней нет никаких мосфетов, следует просто наклеить кусок теплоизоляции такого размера, который представляется вам разумным. Как минимум – больше расстояния между отверстиями для крепления кулера.
После завершения процедуры теплоизоляции следует собрать систему с любым подходящим кулером для проверки – включается ли она и нет ли каких-то непредвиденных глюков.
Полезно организовать дополнительный обдув стакана и материнской платы. Движение воздуха позволит снизить скорость образования конденсата, да и лишнее охлаждение остальных компонентов никогда не будет лишним.
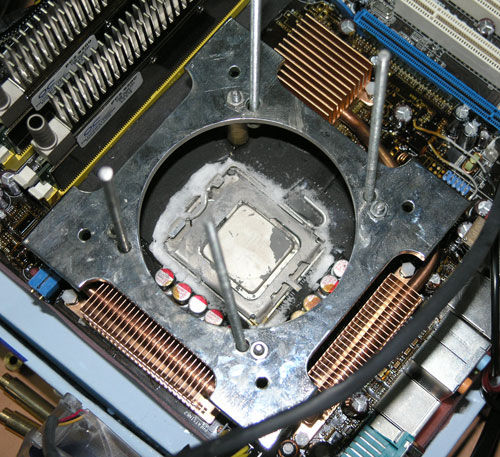
Отдельный вопрос это установка стакана на материнскую плату. Опять таки, стоит признать, что наше решение далеко не идеально. Дело в том, что стакан собирался еще во времена Socket 478 и совместимость с LGA775 пришлось обеспечивать путем изготовления переходника. В результате жесткость сочленения оказалась хуже, чем могла быть. В целом же принцип создания надежного и достаточно простого крепления следующий. Изготавливается акриловое или пластиковое кольцо, внутрь которого устанавливается стакан. Толщина такого кольца чем больше, тем лучше, так как от этого зависит степень возможного перекоса. С помощью длинных болтов стакан крепится к материнской плате, причем с обратной стороны обязательно наличие дополнительной пластины, соединяющей все четыре болта – иначе конструкция, гораздо более тяжелая и габаритная, чем обычный кулер, может повредить плату. Мы взяли пластину от кулера Thermaltake Big Typhoon. Естественно, что крепится такая пластина поверх теплоизоляции, а не под нее.
Установив стакан на материнской плате, следует еще раз провести проверку работоспособности системы. Учтите, что способности пустого стакана по теплоотводу (особенно паяной конструкции с тонким дном) минимальны, так что вряд ли процессоры класса «термоядерная печка», такие как топовые Kentsfield, смогут долго работать – в нашем случае перегрев наступал до загрузки BIOS. Улучшить ситуацию можно, налив в стакан банальной воды – ведь проверить надо всего-лишь одну вещь: может ли ПК пройти POST.
3. Дьюар
Третьей задачей, стоящей перед желающим заняться экстремальным охлаждением, стоит приобретение сосуда Дьюара, то есть контейнера для перевозки жидкого азота. Как ни странно, это, пожалуй, самый сложный пункт для большинства желающих заняться подобными экспериментами, так как сосуды недешевы и продаются сравнительно редко. Конкретных рекомендаций мы дать не можем, так как длительными поисками не занимались. Рискну предположить, что помочь с этим вопросом могут либо на кислородном заводе, либо в организациях, где жидкий азот используют в технических целях в сравнительно небольших количествах (например, в некоторых медучереждениях).Сосуды Дьюара (также просто именуемые «дьюарами») бывают различных емкостей. По нашему мнению, наиболее предпочтительны 15-литровые, так как сочетают достаточный объем с еще вменяемыми габаритами – из такого дьюара несложно наливать одному оператору, в отличие от 30-литровых.
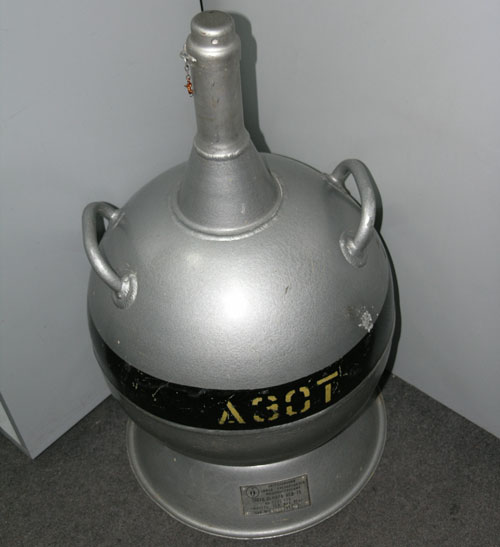
Наш 15-литровый дьюар произведен в далеком 1969 году, но сохранился весьма неплохо, хотя меня иногда посещают мысли о придании ему более сообразного экстремальному предназначению внешнего вида. А что, моддинг дьюаров – новое веяние…
Обращаться с сосудом следует аккуратно, так как внутри он достаточно хрупкий.
В случае, если найти дьюар не представляется возможным, вместо жидкого азота можно поэкспериментировать с сухим льдом – его можно транспортировать в любых теплоизолированных емкостях, например в популярных сумках-холодильниках. Конечно, итоговая температура будет около -70С, да и сама процедура охлаждения несколько отличается и заслуживает отдельного материала (таковой выйдет, если у нас закончится азот и мы перейдем на сухой лед), но рекомендации по изготовлению стакана и теплоизоляции остаются в силе.
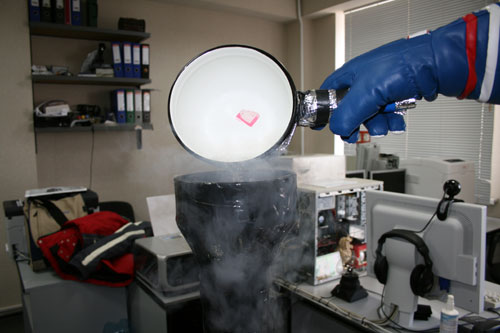
Кроме сосуда Дьюара, для наливания азота в стакан потребуется промежуточная емкость, так как напрямую из 15-литровой цистерны делать это просто невозможно. С точки зрения удобства и эффективности, лучше всего использовать для этого небольшой термос. Проблем с ним две: узкое горлышко заставляет быть достаточно аккуратным при переливании, а отсутствие ручки по началу психологически осложняет процесс, если на руках нет перчаток. Мы же использовали металлический ковш, все внешние поверхности которого (и особенно ручка!) были тщательно теплоизолированы. Такая конструкция упрощает наливание и позволяет вовсе отказаться от перчаток, но из-за большой металлической поверхности азот в ковше начинает мгновенно очень активно кипеть, что повышает расход. В общем, термос все же оптимальнее и в дальнейшем мы будем использовать именно его.
4. Азот
Затем, необходимо приобрести на кислородном заводе необходимое количество азота. В Киеве он стоит $1/литр, при расходе в среднем 3-4 литра на час работы компьютера. По опыту общения с Киевским кислородным заводом, можно сказать следующее: никаких проблем с приобретением азота нет. Тем не менее, так как вопросы социального интерактива регулярно вызывают проблемы у некоторых личностей, я опишу процесс подробнее.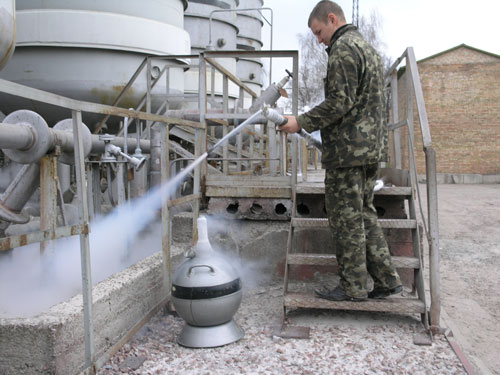
Схема такая: звоните на завод, уточняете время работы человека, ответственного за продажу жидкого азота. Приезжаете (разумеется, на автомобиле – в общественном транспорте с дьюаром не поездишь), узнаете схему проезда до собственно места выдачи азота. Без дьюара приезжать бесполезно, в ведро азот не нальют. Найдя нужного человека, отдаете ему дьюар и он его заполняет. Оплата наличными на месте. Особых вопросов никто задавать не будет, так как для них продажа азота частным лицам в небольших количествах является вполне рутинной. Процедура для 15-литрового сосуда (см. на фото) занимает примерно 10 минут и первый раз за ней наблюдать весьма интересно.
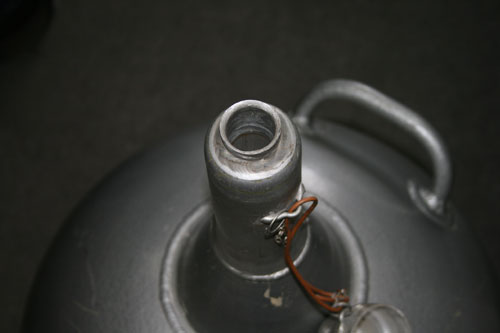
Конструкция крышки на сосуде Дьюара предполагает наличие в ней отверстий, через которые азот испаряется. Дело в том, что будучи налит в сосуд, азот постоянно потихоньку выкипает. В таком дьюаре, как у нас, все содержимое испаряется в течение примерно двух недель, поэтому лучше всего приобретать азот максимум за день-два до планируемой бенчинг-сессии. Заклеивать отверстия на крышке или, тем более, затыкать дьюар герметично нельзя!
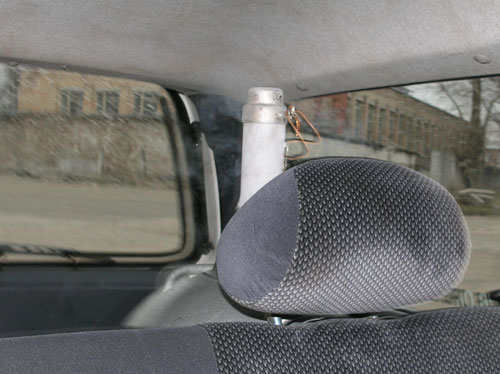
После заполнения некоторое время из дьюара будет идти пар из азота. Он не слишком холодный, и пропадет минут через 15-20. Как прокомментировал это продавец азота на заводе: «Вот вам еще один кондиционер в машину». Везти заполненный дьюар в машине нестрашно, он очень устойчив, хотя, конечно, заниматься стрит-рейсингом не стоит – все же азот в автомобиле должен впрыскиваться в двигатель в виде закиси, а не разливаться по салону из упавшего дьюара. В универсале сосуд можно просто установить в багажник, в других машинах лучше всего поставить его на пол перед сиденьем. Расплескаться от небольшой качки он тоже неспособен, так что сверхпредосторожности не требуются.
Нести заполненный сосуд объемом 15 литров лучше вдвоем, одному это делать очень неудобно. О больших дьюарах я даже не говорю: бенчинг-сессия становится хорошим поводом встретиться с товарищами.
Так как азот постоянно испаряется, хранить его стоит в проветриваемом помещении достаточного объема. В идеале – на открытом балконе. Хотя, ничего страшного в азоте в таких количествах нет. Все наши эксперименты (и хранение заполненного дьюара вплоть до испарения всего содержимого) проводились в комнате Тестовой лаборатории площадью около 40 кв.м, хоть и оборудованной кондиционером и регулярно проветриваемой, но без какого-либо изменения привычного графика проветриваний в связи с азотом – как видите, все живы до сих пор.
5. Железо
И, наконец, надо подобрать подобающее моменту аппаратное обеспечение. Логичнее этот пункт было поставить самым первым, так как о железе обычно заботятся заранее, но с точки зрения важности для организации собственно процесса экстремального охлаждения он, пожалуй, все же на последнем месте.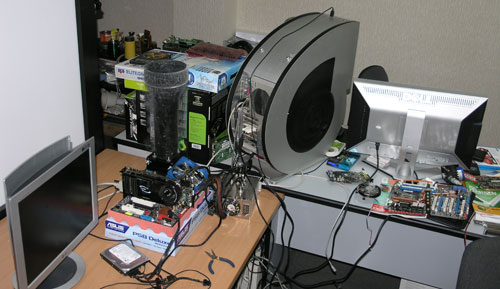
Вначале очень желательно выделить под эксперименты достаточное количество места на столе. Конечно, собрать тестовый стенд можно и в полном беспорядке среди разбросанных процессоров и видеокарт (как это обычно и делается), но все же аккуратность никогда не помешает.
Так как охлаждать мы собрались именно процессор, то главными компонентами будут именно он и материнская плата. Если есть возможность, из имеющихся экземпляров нужно отобрать тот, который будет работать на наибольшей частоте при менее экстремальном охлаждении. Использование в этих целях системы фазового перехода оптимально, но в крайнем случае можно обойтись и тестированием на воздушном кулере или СВО. Очень желательно убедиться в отсутствии так называемого «FSB Wall», опустив множитель до минимального и разгоняя процессор по шине. Заодно, кстати, таким образом (если это еще не сделано) следует определить пределы возможностей материнской платы. Скажем, на процессоре Intel Core 2 Duo E6600 с заблокированным коэффициентом умножения для достижения сравнительно скромных (хорошие экземпляры способны на это под обычным VapoChill LS) 4500 MHz требуется частота FSB 500 MHz. Определить, способна ли на работу в желаемых условиях материнская плата нужно заранее и, при необходимости, провести модификации для улучшения потенциала: как правило, это установка СВО на северный мост и увеличение напряжения на нем путем вольтмода. По возможности не стоит использовать «капризные» материнские платы, которые могут вести себя непредсказуемо в нештатных режимах. По нашему опыту (не только «азотному»), из ныне актуальных плат отменной стабильностью и повторяемостью результатов отличается серия ASUS P5B и особенно Commando. А вот nForce 680i SLI, особенно модели на нереференсном дизайне PCB, склонны к чудачествам – то, чему вы будете менее всего рады при температуре процессора ниже -100С.
Кстати, о температурах. Главным злом для всех экстремальных оверклокеров выступает так называемый “cold bug” – температурное ограничение работы какого-то компонента, когда при снижении температуры ниже определенного предела он перестает стартовать или ведет себя нестабильно. О том, как себя ведут те или иные процессоры, материнские платы и видеокарты можно узнать, изучив ветки в тематических форумах. Например, у Intel Desktop Board D975XBX2 имеется cold bug при -127 градусах, обусловленный спецификой работы системного мониторинга. При подготовке к первым экспериментам мы об этом факте забыли, поэтому потратили несколько часов впустую и, в итоге, добились всего лишь 4300 MHz на не очень удачном сэмпле Core 2 Extreme X6800. Причем побороть cold bug нам удалось немного неортодоксальным и комичным способом, которым я бы хотел поделиться: на дно стакана мы налили грамм 50 кока-колы, чем сильно ухудшили теплоотвод – минимальная температура поднялась с -130С до -70С, что позволило хоть как-то оттестировать процессор. Разумеется, эффективность подобного решения в полной нагрузке была сравнима с обычной одноступенчатой phase-change системой, что и определило скромные результаты, но для первого раза нам гораздо важнее было просто понять принципы организации процесса.
Еще одним важным компонентом является оперативная память. Изучить особенности поведения имеющихся модулей следует тоже заранее, чтобы не отвлекаться на второстепенные задачи во время бенчинг-сессии. В нашем случае мы не стали настраивать подсистему памяти на абсолютно лучшее быстродействие, ограничившись гарантированно работающей конфигурацией. Помните, что при частоте FSB 550 MHz минимально возможная частота DDR2 на многих платах (тех, которые не позволяют выставить в штатном режиме FSB = 266 MHz частоту DDR2-400) составит уже 1100 MHz.
Если вашей целью, как и у нас, являются только тесты CPU, то о высококачественной видеокарте можно не беспокоиться. Более того, некоторые эстеты предпочитают использовать для азотных сессий адаптеры под интерфейс PCI (не PCI-Express) из-за их большей стойкости к повышенным частотам шины. На наш взгляд, с появлением PCI Lock это стало избыточным, но тем не менее, традиция сохраняется. Если же в планы входят и 3D-бенчмарки, также заранее подготовьте видеокарту(-ы): обеспечьте должное охлаждение, при необходимости сделайте вольтмоды, изучите поведение карт в таком режиме – запомните максимальные стабильные частоты и те, на которых сохраняется работоспособность в интересующих тестах.
Требования к блоку питания зависят от выполняемых задач. При отсутствии 3D-нагрузки и, соответственно, мощных видеокарт, вполне можно обойтись качественным современным БП мощностью 500-600 Вт, его должно хватить для обеспечения питанием любого CPU. Стоит подключить БП в максимально возможной конфигурации разъемов (т.е. 24+8 пин предпочтительнее 20+4 пин), включая имеющиеся на некоторых материнских платах дополнительные molex-коннекторы. При высоких напряжениях CPU и огромных частотах нагрузка на систему питания очень высока, так что стоит по максимуму упростить ей жизнь. Если предполагаются бенчинг в 3D, требования к БП растут пропорционально используемым видеокартам. Пожалуй, я не перегну палку, если посоветую использовать в таких целях 1000-ваттные и более мощные блоки.
В целом, к моменту включения ПК с установленным стаканом вы должны иметь идеально собранную и настроенную систему, все особенности поведения которой вы знаете и которой не хватает только дополнительных триста-пятьсот-тысячу мегагерц тактовой частоты CPU, которых нужно достичь с помощью жидкого азота.
6. Программное обеспечение
Думаю излишне говорить, что вышеописанный процесс подготовки тестового стенда предполагает и установку всего комплекта необходимого программного обеспечения. Операционная система должна быть оптимизирована наиболее привычным для вас образом, все драйверы – установлены в наиболее скоростных версиях, их настройки заранее выставлены на предельную производительность. Весь комплект планируемых бенчмарков должен быть работоспособен, а их ярлыки – вынесены на desktop.Кроме того, в арсенале ниндзей жидкого азота имеются две специфических утилиты, не всегда необходимых в других ситуациях. Во-первых, это Clockgen или SetFSB, т.е. софт, позволяющий управлять частотой FSB из Windows. Все процедуры с жидким азотом предполагают старт ПК на сравнительно безопасной частоте и дальнейший разгон программными средствами. Этим экономятся драгоценные минуты, уходящие на перезагрузки и смену настроек BIOS Setup.
Во-вторых, практически обязательным является использование ПО для мониторинга температур, по крайней мере во время поиска пределов работы CPU. Рекомендуем для этого Speedfan, нормально реагирующий на минусовые температуры. Цель использования этого ПО – определение реальных температур в простое и загрузке, их динамики и, при необходимости, мониторинга минимального значения с целью недопущения cold bug.
Процесс в теории и на практике
Сам процесс происходит следующим образом: после тщательной сборки всех компонентов, азот с помощью термоизолированного ковша или термоса заливается из дьюара в стакан, заполняя его примерно наполовину.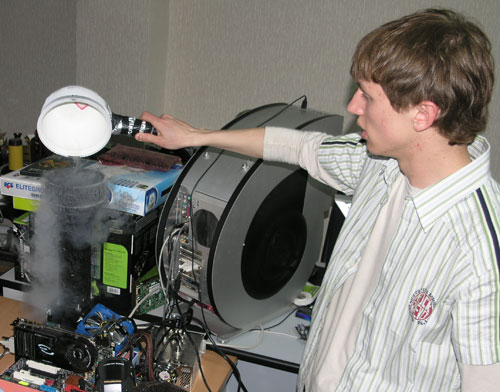
Такой уровень желательно поддерживать на протяжении всей процедуры разгона и тестирования, регулярно подливая азот – именно поэтому должность «кочегара» столь ответственна.
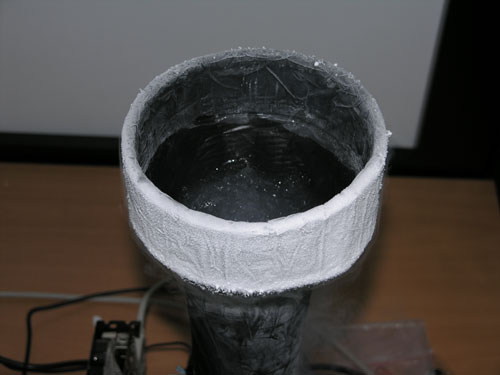
Чем меньше азота в стакане, тем активнее он испаряется, снижая температуры. Зато полный стакан, особенно такой высоты, как у нас, позволяет делать 10-15 минутные перерывы между доливами жидкости.
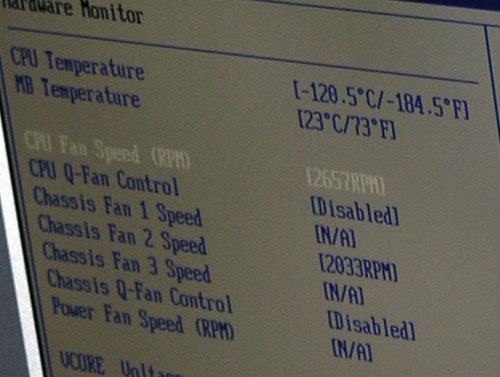
Азот охлаждает процессор до температур, недостижимых другими способами – значительно ниже -100 градусов, таким образом, исключительно позитивно влияя на потенциал разгона.
Рекомендуемый алгоритм действий такой. После включения ПК, в BIOS выставляется необходимый уровень напряжения, коэффициент умножения, разумно высокая частота FSB (такая, на которой CPU будет гарантированно стартовать каждый раз) и прочие параметры. Если вы не знаете нужное значение Vcore, стоит начать с привычного для разгона с другими системами охлаждения, а далее экспериментальным путем установить оптимальное. В нашем случае оно оказалось равным 1,6 В. При более высоких значениях, потенциально ведущих к увеличению потенциала частоты, из-за нелучшей конструкции стакана температура CPU в нагрузке оказывалась выше, чем при 1,6 В, что приводило, напротив, к снижению разгона. Если обеспечить лучший теплоотвод, напряжение можно было бы поднять без ухудшения температурного режима – это одно из направлений улучшения полученного нами результата.
Загрузив на безопасной частоте операционную систему, нужно вначале установить абсолютные пределы разгоняемости CPU. Для этого используется Clockgen или SetFSB, частота в котором плавно поднимается до получения suicide screen CPU-Z. После зависания и ребута процедуру стоит повторить пару раз, чтобы убедиться в повторяемости результатов. Кстати, на всякий случай напомню: подтверждением разгона является не столько скриншот CPU-Z, сколько его валидация – не забывайте сохранять этот файл каждый раз, улучшая результат.
Не мешает на заднем фоне открыть окно Speedfan, чтобы иметь представление о том, как с изменением частоты меняется температура. Стоит также поэкспериментировать с количеством азота в стакане, наблюдая за динамикой температуры в простое при разном уровне жидкости.
Далее ПК следует продолжать загружать с безопасной частоты, но вместо suicide screen начать поиск максимальной частоты прохождения искомых тестов. В качестве тестового приложения рекомендуется Super PI 1M, как наиболее быстрый из сильно загружающих систему. Это также делается плавно, с не слишком большими шагами повышения FSB. В среднем, разница между скриншотом CPU-Z и пределом реальной работоспособности составляет от 100 до 300-400 MHz, причем чем хуже стакан, тем больше будет дельта частот. Если ваша задача – это не Super PI, а нечто иное, то зная максимальную частоту прохождения данного теста, следует перед запуском искомого приложения вначале снизить ее на 100 MHz от максимальной, так как Super PI 1M не очень требователен к стабильности. Если тест пройдет на пониженной частоте – постепенно повышайте, пока не дойдете до предела стабильности. Глобальный принцип прост и отлично формулируется поговоркой: «лучше синица в руке, чем журавль в небе». Лишь добившись неких позитивных результатов, следует пытаться пройти тесты на грани стабильности.
Если это ваш первый эксперимент с азотом – не нацеливайтесь сразу на рекорды. Конечно, все может пройти исключительно успешно, но хорошим результатом для первого раза будут, в первую очередь, не мегагерцы и «попугаи», а просто накопление опыта и понимание процесса на практике.
Результаты
Как уже ясно из текста, мы провели две сессии, которые разделяла пара недель. В первый раз, используя материнскую плату Intel D975XBX2 и процессоры Intel Core 2 Extreme QX6700 и X6800, ничего выдающегося (кроме стабильной работы на 4300 MHz, т.е. всего на 200 MHz выше, чем с VapoChill LS) мы не достигли по причине cold bug и нескольких других промашек.Второй раз мы собрали тестовый стенд заново, используя уже проверенные компоненты:
Процессор: Intel Core 2 Duo E6600 (Conroe, 2,4 GHz)
Система охлаждения: жидкий азот
Материнская плата: ASUS P5B Deluxe (Intel P965)
Оперативная память: 2x1024 MB OCZ PC2-9200 FlexXLC Edition
Видеокарта: EVGA e-GeForce 8800 GTX
Жесткий диск: Seagate Barracuda 7200.9 80 GB
Блок питания: HIPER Type-R HPU-7S730
Операционная система: MS Windows XP Pro SP2
Проводя подобное (если не считать первого эксперимента) тестирование впервые, мы решили сосредоточиться на сугубо процессорных тестах и отложить бенчинг в 3DMark до следующего раза.
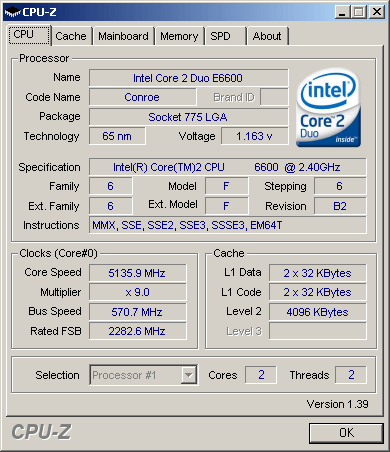
В итоге, для скриншота CPU-Z мы смогли достичь частоты 5135 MHz у процессора на ядре Conroe, 15 результат в мире для Intel Core 2 Duo E6600.
Стабильная работа в тесте Super PI была достигнута на частоте 4980 MHz, что позволило получить результат 10,391 секунды и попасть в ТОР-100 рейтинга HwBot в этой дисциплине.
Второй схожий тест, Hexus PiFast, был работоспособен на частоте 4800 MHz, но наше достижение вошло в TOP-50 рейтинга HwBot для данного теста.
Откровенно говоря, каждый из результатов мог бы быть лучше: операционная система не была специально оптимизирована под Super PI/PiFast, да и валидацию 5200 MHz тоже можно было бы со второго-третьего раза получить, чего мы не сделали… Однако, какие-то мегарекорды «здесь и сейчас» не были нашей целью для данной сессии. В отличие от первого раза, мы получили необходимый опыт для эффективного тестирования процессоров под жидким азотом – опыт, который мы еще не раз будем использовать на следующих поколениях CPU. Вот тогда и поговорим о рекордах.
Credits
Несмотря на кажущуюся простоту описанных действий, для того, чтобы реализовать задуманное, потребовались усилия всего киевского подразделения Team MXS – в организации бенчинг-сессии принимало участие более пяти человек! Пользуясь возможностью, перечислю всех участников и их вклад:- как уже сказано было ранее, стакан для азота изготовил наш мегамастер Давид «VER-VOLF» Хачатрян, он же еще несколько лет назад где-то добыл сосуд Дьюара;
- один из двух капитанов Team MXS, Андрей “BuM!!!” Лунин час за часом работал на ответственнейшей должности «кочегара», заполняя стакан азотом;
- Василию «Vasiliy» Стаськову, хорошо известному посетителям нашего форума и читателям «Компьютерного обозрения», высказывается благодарность за неоднократные поездки на кислородный завод с дьюаром в багажнике его машины;
- материнскую плату ASUS P5B Deluxe предоставил наш друг с сайта Topmods.net Илья "TiN" Цеменко, также принимавший участие в мероприятии в качестве оператора тестового стенда (кому, как не владельцу материнской платы, лучше всего знать её поведение?);
- владелец оттестированного экземпляра процессора Intel Core 2 Duo E6600 с отличным потенциалом разгона - Алексей "ApocaLeXX" Батуро (Москва). TiN же привёз собственно процессор в Киев;
- главный редактор ModLabs.net, Олег «cyclone» Голубович выполнял роль оператора в первой сессии, когда мы мучали бедный Intel D975XBX2;
- заглянувшие на огонек коллеги с сайта Overclockers.com.ua, Qntality и SArd, помогали BuM!!! в его нелегкой работе кочегаром. Увы, их поезд не стал задерживаться по поводу проведения нашей сессии экстремального разгона, поэтому наши друзья были вынуждены покинуть Тестовую лабораторию задолго до окончания эксперимента;
- ну и я, то есть ALT-F13, в качестве организатора сего действа, добытчика азота и, при необходимости, оператора стенда (да-да, только на моей воле к победе был получен хороший результат в PiFast, когда TiN призывал эту затею бросить :-P) и кочегара.
Что дальше?
Конечно, на полученных (откровенно говоря, достаточно скромных, с учетом наших амбиций) результатах мы останавливаться не собираемся. Дальнейшие планы по улучшению наших достижений включают следующее: новый стакан для CPU, построенный с учетом рекомендаций других разработчиков; стаканы для GPU (в т.ч. для SLI/CrossFire-комбинаций), что позволит нам бороться за высокие места в 3D-рейтингах; ну и, конечно же, новые процессоры для тестового стенда – как новинки, так и банальные Celeron D (Cedar Mill), ведь именно это семейство отличается способностью к максимальному разгону в мегагерцах. 5 GHz @ Conroe есть, теперь будем штурмовать 8 GHz @ Cedar Mill… А как иначе? Ведь Team MXS ModLabs.net срочно нуждается в новых достижениях ее членов!Ваши пожелания и замечания по данному материалу принимаются в соответствующей ветке форума ModLabs.net.
Введение
Элементарный разгон компьютерных комплектующих - вполне обыденное явление, которым сегодня большинство пользователей уже не удивишь. Гораздо более интересной представляется тема экстремального оверклокинга и бенчмаркинга для покорения мировых вершин в табелях о рангах видеокарт, процессоров и т.п. Конечно, для того, чтобы быть первыми, сегодня для успешного разгона комплектующих зачастую уже недостаточно ни воздушного, ни водяного охлаждения. Мировые легенды оверклокинга длительное время используют системы фазового перехода и самый экстремальный способ получения сверхнизких температур - конструкции, хладагентами в которых выступают жидкий азот или сухой лёд. Использование последних связано с определенными трудностями, а при необходимости длительной работы за компьютером становится практически невозможным. Поэтому самый важный шаг для желающих добиться максимального разгона комплектующих и обеспечить их стабильную и продолжительную работу в таком режиме - приобретение или создание собственными руками системы фазового перехода (т.н. фреонки). Зайти в магазин и купить - задача нетривиальная. Гораздо более интересно и познавательно лично пройти весь процесс создания фреонки (желательно - своими руками). Для этого не нужно сверхспособностей и сверхвозможностей. Главное - наличие желания, определенных навыков и теоретических познаний. Первое практически полностью ложится на плечи энтузиаста, второе приобретается со временем, третье - находится в различных изданиях, на страницах сайтов, в специализированных ветках конференций. Если Вы уже прочитали все, что могли, но ничего оптимального для себя в итоге не вывели (не путать с ситуацией, в которой оказался автор печальноизвестной «Фреонки за 7 дней»:) ), или хотите ограничиться прочтением нескольких правильных статей на тему построения фреонки своими руками, данный материал - для Вас! В нем собраны основные вопросы, которые могут возникнуть у новичков при создании экстремального охлаждения. Однако нужно учитывать, что материал рассчитан на относительно подготовленных пользователей, поэтому для начала нужно проштудировать парочку хороших статей или страниц популярных форумов на заданную тему.Надеемся, что наш FAQ поможет Вам снять все (или хотя бы большинство) вопросов при изготовлении системы фазового перехода!
Содержание:
1. Компрессоры
2. Конденсаторы
3. Хладагенты
4. Испарители
8. Пайка и все, что с ней связано
9. Вакуумирование и заправка
10. Изоляция
11. Другие вопросы
12. Краткий словарь терминов по phase-change системам
13. Дополнительная информация
Компрессоры
Q: Я хочу купить компрессор, но не могу определиться с характеристиками. Продуктам какого производителя следует отдавать предпочтение?A: Прежде всего, Вам следует определиться с желаемыми характеристиками собираемого устройства. Необходимо учитывать:
- ориентировочное тепловыделение процессора/видеокарты;
- температуру, которую Вы хотите получить в нагрузке;
- бюджет проекта.
Выбирать компрессор нужно, руководствуясь как минимум вышеприведенными критериями. Только при грамотном подходе к данному вопросу есть большой шанс, что покупка оправдает себя на все 100%.
Необходимо помнить, что в большинстве самодельных систем фазового перехода используются поршневые герметичные низкотемпературные компрессоры :)
Краткая характеристика продуктов некоторых вендоров:
Embraco Aspera (Словакия) - выпускает тихие и производительные компрессоры, которые пользуются популярностью у фреонщиков благодаря хорошему соотношению "цена/производительность".
Danfoss group (Дания) – мировой лидер в сфере холодильного оборудования, известен во многом благодаря отменному качеству выпускаемой продукции. Правда, за него придется доплатить: компрессоры данного бренда стоят на 15-20% дороже аналогов, сопоставимых по производительности.
ЗАО «АТЛАНТ» (Беларусь) - хорошо известный жителям постсоветского пространства производитель. Выпускает широкий модельный ряд компрессоров для холодильников. По характеристикам для создания систем фазового перехода подходят лишь старшие модели. Но даже на них трудно получить хороший результат.
TECUMSEH EUROPE / L'unite HERMETIQUE (Франция) – весьма интересный производитель. Правда, статистика по использованию его продуктов в самодельных фреонках довольно скудна, поэтому рано подводить какие-то глобальные итоги. Можно лишь сказать, что эти изделия обладают неплохим соотношением "цена/производительность", но шум у них выше, чем у продуктов от тех же Aspera или Danfoss.
ACC (Electrolux) (Испания) – довольно редкий гость в одноконтурных фреонках, но старшие модели получили широкое распространение в составе каскадов. Шум, как и мощность, у них на высоте.
Q: Из компрессора выходят три трубки. Какая из них за что отвечает?
A: для того, чтобы разобраться в данном вопросе, необходимо:
1. Посмотреть документацию на Вашу модель компрессора. Она обычно располагается на официальном сайте производителя.
2. Если документации нет, то назначение каждой из трубок можно определить самому. Две из них работают на всасывание, а третья - на нагнетание. Точно определить, где какая, можно, заткнув пробкой трубку самого большого диаметра, и кратковременно включив компрессор. Откуда подует воздух – нагнетающая (высокое давление), а там, где он втягивается – всасывающая (низкое давление).
Та трубка, которая была закрыта пробкой, используется для заправки.
Q: Купил компрессор, а внутри что-то колышется и бьётся об стенки. Что это значит?
A: Скорее всего, у Вашего компрессора не закреплена обмотка. Это - нормальное явление, по данному поводу не стоит беспокоиться.
Q: Как определить, какое масло заправлено в компрессор? И с каким типом фреона оно совместимо?
A: На наклейке компрессора указан тип используемого масла.
Ниже приведены классификация и список совместимости различных масел и фреонов:
1. Минеральные масла:
- нафтеновые;
- парафиновые.
2. Синтетические масла:
Алкилбензольные (А) используются в холодильной промышленности более 25 лет, термически стабильны, хорошо смешиваются с хладагентами групп ХФУ, ГХФУ.
Полиалкилгликольные масла (ПАГ) широко используются в мобильных установках, таких как автомобильные кондиционеры с хладагентом R134A.
Полиолэфирные масла (ПОЕ) рекомендуются для установок с хладагентами группы ГФУ – R134, R407C, R410A, R404A.
3. Полусинтетические масла представляют собой смеси алкилбензольного и минерального масел (А/М).
Подробнее о совместимости масел вы можете прочесть в этом файле
Q: Какая безопасная температура эксплуатации компрессора?
Нормальной рабочей температурой для поршневого компрессора является 60-70? С, его обдув обязателен.
Остудить компрессор можно несколькими способами:
- Заправить немного больше фреона, чем нужно. В результате будет обмерзать входящий в компрессор патрубок.
- Расположить компрессор за конденсатором (стандартное расположение), чтобы он обдувался вентилятором.
Q: Я приобрел компрессор, но не знаю, как его подключить
A: Здесь подробно расписаны все действия в данной ситуации (иллюстрации прилагаются).
Q: Как менять масло в компрессоре?
A: У обычных поршневых компрессоров масло заменяется достаточно просто: старое сливается или всасывается (с помощью груши) через один из патрубков. Новое заправляется «обратным» путем.
Если же возникли какие-то проблемы, а приведённым выше способом полностью удалить всё масло не получается, можно возле картера компрессора просверлить отверстие, через которое и вылить старую жидкость. Через эту же дырку заливается новое масло. После этого отверстие заваривается.
Q: Можно ли в самодельных фреонках использовать старые компрессоры от холодильников, кондиционеров?
A: Да. Для начала вы должны узнать, компрессор какой мощности возможно достать, и на каком газе он работает. Если данное изделие удовлетворяет Вашим требованиям, то можно попытаться использовать его. Правда, стоит учесть такие факторы:
- Компрессоры от старых холодильников не обладают достаточной мощностью, чтобы заморозить бутылку пива, так что об охлаждении процессора не может быть и речи
- Роторные высокотемпературные компрессоры (используются в кондиционерах БК) предпочтительнее при сборке системы фазового перехода, но даже на них хорошие результаты получить крайне сложно.
Бюджетная фреонка - миф или реальность
Экстрим для бедных или фреонка даром
Конденсаторы
Q: У меня есть конденсатор от старого холодильника/кондиционера, но в нём остались масло и мусор. Чем его можно промыть?A: Для промывки можно использовать четыреххлористый углерод или специальные промывочные фреоны марок R11, R140B, R-113.
Q: Как мне узнать мощность конденсатора?
A: Данную величину можно рассчитать по формуле.
Сперва узнаём [площадь оребрения – высота (м)] х [глубина (м)] х [кол-во ребер на один сантиметр] х [ширина (см)] х 2
Потом рассчитываем мощность: [площадь (м)] х [коэффициент теплообмена (30)] x [разница температур конденсации фреона и продуваемого воздуха (° C)].
Q: Я - обладатель конденсатора Lu-Ve. У него очень плохо паяются патрубки. С чем это связано?
A: У Lu-Ve в модельном ряду представлено несколько видов конденсаторов. В самых младших моделях патрубки не медные, как может показаться, а стальные (медное лишь напыление). Поэтому их нужно паять с использованием специального флюса.
Q: Какие ограничения налагаются на размер/структуру конденсатора?
A: Главное, чтобы конденсатор мог отвести нужное количество тепла (пример расчета - выше). При сборке ультра-компактной фреонки допустимо использование радиаторов от систем водяного охлаждения (пример: Thermaltake CL-W0021). Еще одно требование – конденсатор должен быть многопроходным и выдерживать большое давление.
Хладагенты
Q: Как рассчитать длину капилляра?A: Точную длину капилляра, как и количество хладагента в системе, рассчитать невозможно. Поэтому Гарри Ллойд (Gary Lloyd) составил данную таблицу с примерными соотношениями длины/диаметра капилляров для разных фреонов и мощности нагрузки:
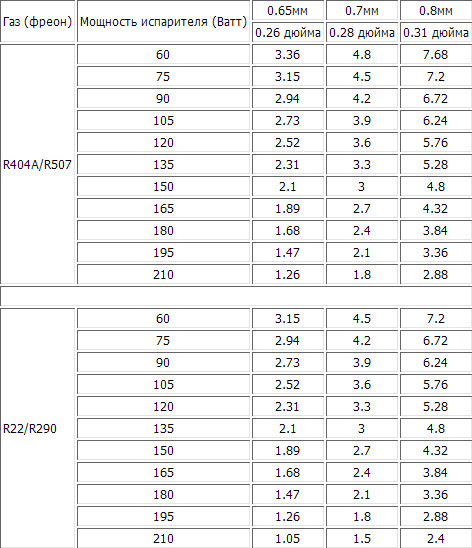
Более правильные данные можно получить самостоятельно, воспользовавшись программой, написанной Boud. Скачать её можно здесь.
Следует добавить, что подбирать количество фреона и длину капилляра экспериментальным путём следует аккуратно. Не забывайте: при большом количестве хладагента он может испаряться неполностью и попадать в жидком виде в компрессор, что приведёт к поломке последнего. Чтобы решить такую проблему, иногда для перестраховки (в ущерб производительности) ставят докипатель. В нём не испарившийся фреон полностью выкипает, и не попадает в жидком состоянии в компрессор.
Q: Где можно посмотреть характеристики фреонов?
A: В этом документе сосредоточены все основные данные о фреонах.
Испарители
Q: Можно сделать систему на два испарителя с одним компрессором?A: Да. Но у этой конструкции есть существенные недостаток - не возможности контролировать равномерную подачу фреона в оба испарителя. Из-за этого возникает постоянный перепад температур на испарителях. Единственным идеально пригодным местом для эксплуатации данного типа систем является охлаждение тандема видеокарт, работающих в режиме SLI или CrossFire.
Q: Какие конструкции испарителей предпочтительнее?
A: Здесь Вы можете изучить структуру уже готовых испарителей и выбрать оптимальный для себя вариант.
Q: Как проверить испаритель на течи (опрессовать)?
A: После того как испаритель спаян в единую конструкцию и отмыт от окалины, нужно впаять в него клапан Шредера (предварительно выкрутив из него ниппель), и накачать фреоном. Затем погрузить конструкцию в воду. Если где-то происходит «протечка» фреона, то пометьте нужное место маркером, выпустите хладагент, и пропаяйте еще раз место протекания, не жалея припоя.
Изоляция
Q: Какие виды изоляции существуют?A: K-Flex – самый распространенный и популярный в наших краях вид изоляции. Диапазон рабочих температур: от -200° до +105? С.
Armaflex – еще один дешёвый и достаточно качественный вид изоляции. Диапазон рабочих температур: от -50? до +105? С.
Neoprene – труднодоступен и дорог, но обладает наилучшими среди изоляторов характеристиками, работает в широком диапазоне температур.
Q: Как предотвратить образование конденсата вокруг процессорного разъема?
A: Обычно теплоизоляции поддаётся наиболее чувствительная к образованию конденсата зона - примерно 15 см по периметру процессорного сокета. Выполнить её можно такими способами:
- Теплоизоляционные материалы – наиболее простой и наименее трудоёмкий способ изоляции. Если Ваша система собирается для кратковременного использования, можете смело использовать данный метод, не применяя диэлектрики и тому подобное. Примечаине: Листовая теплоизоляции довольно дорога, поэтому предпочтительнее и выгоднее использовать разрезанную трубчатую изоляцию большого диаметра.
- Теплоизоляционные материалы + вазелин/токонепроводящий лак/силикон – наиболее сложный способ, используется при эксплуатации компьютера 24/7. В тех случаях, где на первое место выходит надёжность, он является самым предпочтительным вариантом (правда, не исключено, что при качественно выполненной изоляции можно обойтись без применения диэлектриков).
- Теплоизоляционные материалы + нагреватели – применяётся в серийных системах, где вокруг процессорного разъема устанавливаются маломощные нагреватели (1-4 Вт), которые предотвращают образование конденсата.
Пайка и все, что с ней связано
Q: Я хочу собрать пропано-кислородную горелку. Что мне для этого нужно?A:
1. Кислородный баллон и редуктор к нему
2. Пропановый баллон и редуктор
3. Горелка
4. Шланги
Примечание: Редукторы служат для понижения и выравнивания давления на выходе из баллонов.
Q: Какими еще разновидностями горелок можно паять?
A: Для пайки меди подходят такие:
1. Турбо-пропан. Состоит из специальной горелки и пропанового баллона. Неплохой вариант, имеет достаточную температуру горения для прогрева испарителя, но если конструкция достаточно массивная, придется прибегнуть к помощи плиты.
2. МАПП газ и горелка под него. Имеет температуру горения 1300 градусов Цельсия, обладает достаточной мощностью для пайки трубок. Спаять испаритель им тоже возможно, но для этого объект пайки потребуется дополнительно разогревать на плите.
3. Пропан-кислород. С помощью этой горелки вы сможете паять всё — от ювелирной пайки маленьких деталей и швов до тяжелых и габаритных испарителей, конденсаторов и т.д.
Q: Какие типы припоя существуют?
A: Для пайки соединений типа «медь-медь» можно использовать самый дешёвый медно-фосфорный припой. Если же Вам предстоит паять разнотипные металлы, то придется использовать припой с содержанием серебра:
1. Припой с 5% серебра + флюс
2. Припой с 30-45% серебра - чаще данный вид припоя идёт уже офлюсованный
Q: Для чего нужен флюс?
A: Чтобы растворить оксидную плёнку, образовавшуюся на металле во время разогрева конструкции.
Q: Как избавиться от нагара после пайки?
A:
1. Внешний нагар счистить наждачной бумагой.
2. Если он находится в труднодоступных местах (внутри испарителя), то:
- проварить испаритель в концентрированной кислоте;
- проварить испаритель в Coca-Cola; присутствующая в ней кислота прекрасно отмывает как ржавчину, так и нагар.
A: Необходимо отметить то, что патрубки очень сложно прогреть привычным МАПП газом, не используя хотя бы две горелки одновременно. Идеальным вариантом для такой работы остаётся пропан-кислородная установка.
При соединении трубок желательно использовать припой с содержанием серебра. Для получения необходимого качественного эффекта без лишних затрат сил и материалов трубку вначале необходимо нагреть. Тепло с нее будет передаваться на фиттинг компрессора. Горелку необходимо переместить к месту соединения, предварительно нанеся припой. После его растекания можно дополнительно недолго погреть фиттинг компрессора. Напоследок на горячий металл можно нанести еще чуть-чуть припоя для получения идеального (в плане качества соединения и внешнего вида) шва.
Вакуумирование и заправка
Q: Зачем вакуумировать систему?A: Чтобы выкачать из системы весь воздух, а вместе с ним и влагу. Их наличие может вызвать замерзание жидкости в капилляре и, как следствие, нестабильную работу системы.
Q: Чем можно вакуумировать контур?
A: Специальным вакуумным насосом или дополнительным компрессором.
Q: Как вакуумировать систему компрессором?
A: Подключаем вакуумирующий компрессор к клапану Шредера на обратной линии, включаем его. С помощью манометра необходимо следить за падением давления. Когда оно опустится до нижней отметки, включаем на несколько минут основной компрессор. Таким способом можно получить достаточно глубокий вакуум.
Q: Как заправлять систему?
A: После вакуумирования нужно подключить баллон с фреоном к клапану Шредера на всасывающей магистрали, включить компрессор и маленькими порциями подавать фреон в систему. Когда испаритель начнёт запотевать, прекратить подачу фреона и подождать, когда его температура упадёт до минимума, после этого добавить еще немного фреона чтобы температура поднялась на несколько градусов.
Q: Как подключить манометрическую станцию к клапану Шредера?
A: Манометр высокого давления (красный) отвечает за линию компрессор-конденсатор, манометр низкого давления (синий) - испаритель-компрессор.
Аналогично и со шлангами: синий подключается к линии низкого давления, а красный – к линии высокого. Жёлтый служит для заправки и вакуумирования системы.
Q: Как проверить систему на течь?
A: Это можно сделать несколькими способами:
1. Завакуумировать контур и оставить его без работы на несколько дней. После этого по манометрам проследить за изменением давления и сделать соответствующие выводы.
2. Запустить в систему немного фреона и проверить специальным прибором для обнаружения течей («нюхалка»). Помните: он не даёт 100% гарантии отсутствия течей.
3. Надуть контур фреоном, и промазать места пайки мыльным раствором (или раствором Fairy).
Если течи присутствуют, то место их расположения нужно хорошо пропаять, не жалея припоя.
Другие вопросы
Q: Можно как-то сохранить дорогостоящий фреон в контуре при его разборке?A: Для этого Вам изначально придется впаять вентили на входе и выходе из конденсатора. После этого, перекрыв вентиль на выходе, включить компрессор, и он загонит весь фреон внутрь конденсатора. Через несколько минут можете выключить компрессор и перекрыть вентиль на входе.
Q: Что можно использовать в качестве отсасывающего шланга?
A:
1. Медную трубку
- - плохо гнётся;
- - передаёт вибрацию;
- - сложна в эксплуатации;
- + очень надёжная;
- + наиболее дешёвый вариант.
- - высокая стоимость;
- - трудно паяется;
- - имеет свойство растягиваться на 3-5% во время простоя системы;
- + очень гибкая;
- + бывают разной длины;
- + не выпускает из системы хладагент;
- + оптимальные качества для "фреонки".
- - медленно пропускает фреон;
- - «дубеет» при минусовых температурах;
- - не рекомендуется к использованию;
- + дёшевый;
- + легкодоступен
A: Алюминий, медь, фторопласт. Также прекрасно подходят шляпки от гвоздей для прибивания шифера.
Q: Какую термопасту можно использовать при работе процессора в экстремальных условиях?
A: Наиболее приспособлены к относительно низким температурам (до -50? С) следующие распространенные термоинтерфейсы: КПТ-8, НС-125 и Arctic Silver Ceramique (последняя является самым лучшим выбором).
Q: Что такое маслоотделитель? И когда его нужно использовать?
A: Прибор, устанавливаемый на нагнетательной магистрали компрессора перед конденсатором, служит для отделения и возврата масла в компрессор. Именно его называют маслоотделителем. Установка целесообразна только в автокаскадах или многоконтурных системах.
Q: Какой фильтр-осушитель мне купить?
A: Оптимальный выбор для новичка - стандартный литой медный фильтр диаметром 20 мм. Устройства большего объема ((отличаются между собой лишь объёмом цеалита) вряд ли потребуются в одноступенчатой системе. Производители рекомендуют менять фильтр после каждой разборки системы. Реально же на одном устройстве можно прожить две-три реинкарнации системы.
Q: Для чего предназначено смотровое стекло?
A: Для определения степени наполнения системы хладагентом и его степени влажности (на стекле расположен индикатор влажности). Оно являет собой отдельную часть контура фреонки и ставится по желанию сборщика.
Краткий словарь терминов по phase-change системам
Примечание: данный глоссарий позаимствован с ПС Sladky после получения официального согласия автора.Фреон (хладагент) – вещество, циркулирующее по системе фазового перехода. Способно аккумулировать тепло в одном месте контура, транспортировать и отдавать в другом.
Фреонка – тепловой насос. Устройство, работающее на основе фазового перехода хладагента (фреона). Отбирает тепло в одном месте (испаритель) и отдает в другом (конденсатор).
Чиллер - фреонка, испаритель которой охлаждает некий промежуточный теплоноситель (например, жидкость в системе ЖО), и уже этот теплоноситель охлаждает соответствующие элементы системного блока.
Компрессор – основная часть системы фазового перехода. Предназначен для циркуляционной прокачки газообразного хладагента по системе с одновременным сжатием для последующей конденсации в конденсаторе.
Картер компрессора – нижняя часть компрессора, в которой находится масло, смазывающее и охлаждающее механизмы устройства.
Конденсатор (конденсер) – радиатор, в котором сжатый газ охлаждается и конденсируется в жидкость (меняет фазу из газа в жидкость). При конденсации выделяется тепло, которое рассеивается радиатором во внешнюю среду.
Фильтр-осушитель – расположен после конденсатора. Необходим для фильтрации циркулирующего хладагента от механического мусора и удаления воды из контура, случайно попавшей в систему.
Капилляр – один из распространенных дросселей в системах фазового перехода. Представляет собой тонкую длинную медную трубку. Необходим для разделения контура на области высокого и низкого давления. Очень популярен, т.к. степень дросселирования легко настраивается длиной капилляра. Стандартный внутренний диаметр применяемых во фреонках - 0.78 мм.
ТРВ – терморегулирующий вентиль (используется вместо капилляра). Автоматика, призванная удерживать постоянной температуру охлаждаемого объекта. Имеет датчик и по нему автоматически регулирует подачу хладагента.
Испаритель – емкость для выкипания жидкого фреона, охлаждающий элемент. Обычно делается из меди.
Отсасывающая трубка – в большинстве случаев мягкая стальная гофрированная труба для отвода газоподобного хладагента из испарителя. Диаметр - от 8 до 15 мм.
Прямой поток – линия высокого давления системы. Находится на отрезке от компрессора до дросселя (капилляра). По этой линии хладагент движется к испарителю.
Обратный поток – линия низкого давления системы. Находится на отрезке от испарителя до компрессора. По ней хладагент движется от испарителя.
Ресивер – аккумулятор. Ставится после конденсатора на прямом потоке. Необходим для аккумуляции жидкого хладагента на случай возникновения резкой нагрузки и подачи большого количества фреона в испаритель. Обычно используется только в больших промышленных системах.
Докипатель – некая емкость для выкипания жидкого хладагента (остатков, не испарившихся в испарителе) в целях предотвращения попадания жидкости в компрессор. Учитывая малую заправку кустарных фреонок, докипатель обычно не используется. Его роль играют отсасывающая трубка и картер компрессора.
Клапан-шредер (Заправочный штуцер) – штуцер для заправки и вакуумирования системы. Аналогичен автомобильному ниппелю.
Пусковая автоматика компрессора – автоматика, необходимая для запуска компрессора. Обычно сам компрессор имеет 3 контакта, которые питают основную и стартовую обмотки. Автоматика при запуске на короткое время запускает стартовую обмотку. Без этого компрессор неработоспособен. Если различные виды автоматики, с пусковым конденсатором и без (зависит от типа компрессора).
Вакуумный насос – газовый насос, предназначенный для вакуумирования системы перед заправкой хладагентом. Вакуумирование удаляет воздух и влагу, попавшую в систему вместе с воздухом.
Теплоизоляция – пористый материал искусственного происхождения. Необходим для теплоизоляции компонентов системы и предотвращения выпадения конденсата. Основная цель – не допустить притока воздуха к объекту.
Каскад – многоуровневая фреонка. Испаритель внешнего контура охлаждает конденсатор внутреннего. Таким образом, возможно построение нескольких контуров и получение очень низких температур. На одном контуре возможно получение перепада максимум в 50-80? С. В каждом отдельном контуре есть все элементы обычной фреонки, включая компрессор, конденсатор, испаритель…
Автокаскад – многоконтурная фреонка на одном компрессоре, заправленная смесью газов. Газы подбираются с различной температурой кипения и при помощи специальных отделителей работают каждый в своем контуре, после чего объединяются. Компрессор общий, прокачивает рабочую смесь.
Соленоид (электромагнитная муфта) – электрический кран. Имеет 2 положения: открыт и закрыт. Управляется извне электрическим сигналом.
Единицы измерения:
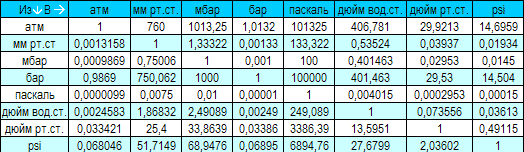
При построении FAQ использованы материалы:
- Голоссарий по фреонкам (автор - Sladky)
- Немного экстрима или фреонка своими руками
- Немного экстрима или фреонка своими руками (2)
- www.chillers.ru
- www.iceberg.ru
Отзывы, пожелания и замечания по данному материалу принимаются в соответствующей ветке форума ModLabs.net.
В моем случае (материнская плата DFI NF4-SLI-DR) упомянутая система охлаждения - самая громкая вещь в ПК (конечно, не считая аккустики:)). Но решить проблему, как большинство – установкой крупного пассивного радиатора (например, Zalman NB-47), не получится. Виной тому - разводка платы. Думаю, читатели помнят (или знают по собственному опыту), что прямо над чипсетом в платах семейства nForce 4 Series зачастую находится видеокарта. Просвет между поверхностью чипа и платой установленной в систему видеокарты составляет всего 12мм. Выхода нет – делаем водоблок. Он заодно поможет хорошенько снизить температуру чипсета и увеличить оверклокерский потенциал материнской платы.
Поскольку тепловыделение, с которым придется бороться, относительно мало, сложной структуры и максимальной эффективности от водоблока не требуется, - подойдет и классическая «змейка». Материал – естественно, медь.
После изучения всех оптимальных вариантов, пришел к выводу, что самым простым и удобным в данном случае будет теплосъемник U-образного внутреннего строения, с выходами в горизонтальной плоскости. Осмотрев место крепления на материнской плате, было решено немного «задрать» выходы для штуцеров под уголом 15-20 градусов, дабы мелкие компоненты элементной базы DFI NF4-SLI-DR не мешали установке продукта народного инженерного мастерства на положенное ему место.
Заготовка, из которой будет изготовлено основание, имеет размеры 40х40х10 миллиметров:
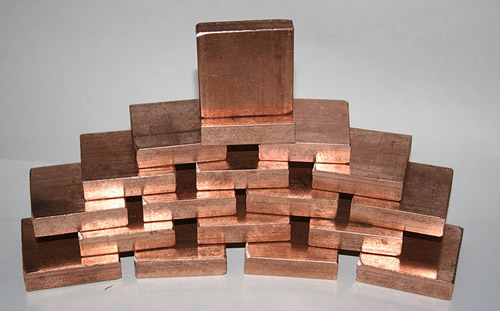
Работу буду проводить подручными средствами (дрель, тиски, прямые руки), поскольку задача проста и не требует большой точности:
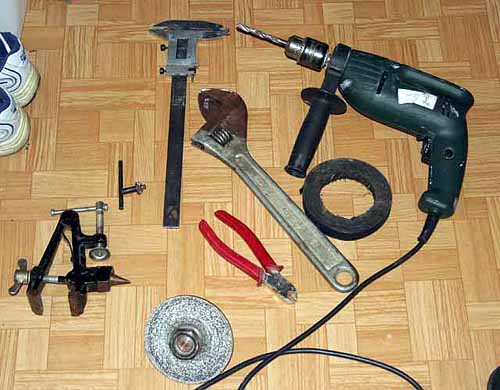
Так как я не хочу создавать лишнее сопротивление потоку воды в контуре СВО, делаем широкий канал с простейшей плоской структурой. Вего полчаса работы, основной инструмент – электродрель со сверлом по металлу диаметром 12мм, и заготовка находится в нужной кондиции:
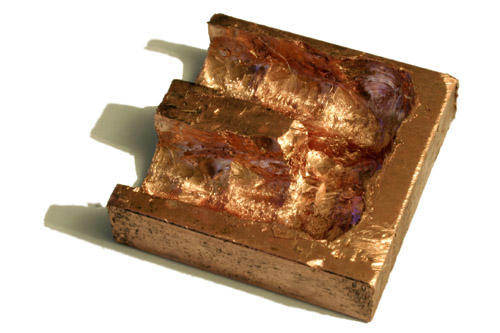
Дно ватерблока будет иметь толщину всего два миллиметра, и в данном случае этого более чем достаточно, учитывая и относительно большой размер кристалла, и то количество тепла, которое необходимо отводить.
Полная конструкция состоит из нескольких частей. Основные из них – вышеприведенный шедевр, а также пластина для крепления, по совместительству являющаяся крышкой, и пара небольших отрезков медной трубки диаметром 12мм – «штуцеры»:
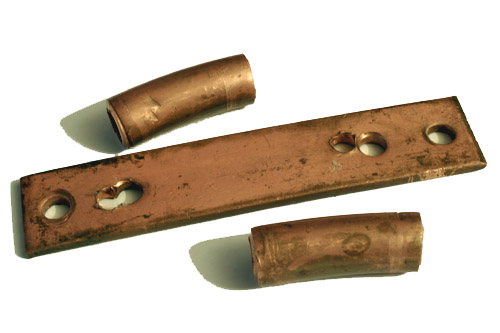
В сборе должно получиться нечто подобное:
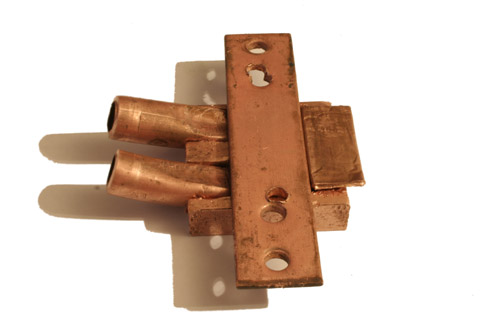
а так подгонялись «штуцера»:
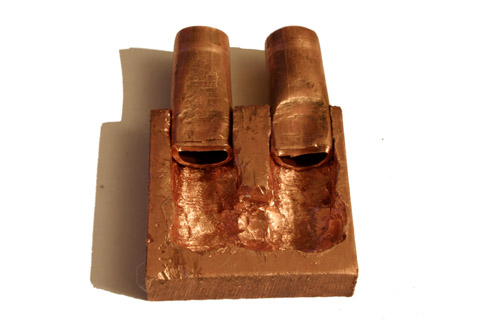
Как Вы наверно догадались, соединяться между собой все детали будут посредством пайки. Было решено паять компоненты ватерблока горелкой и тугоплавким припоем.
Уверен, такой способ может обеспечить полную герметичность всех швов. В работе можно обойтись без флюса, т.к. каждая деталь изготовлена из чистой технической меди. Для начала необходимо основательно прогреть детали, а после этого быстрыми и точными движениями провести по местам швов прутком припоя.
Горелки с MAPP газом в этот момент у меня не было, пришлось достать из «чулана» свою первую горелку:

Работать ей легко и просто, но для начала надо «набить руку», тренируясь «на кошках»:). После обретения некоторой сноровки все пойдет как по маслу. Главное - основательно прогреть деталь:
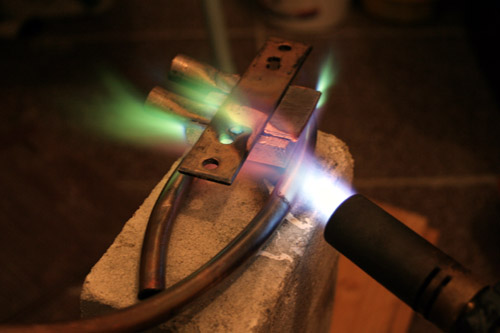
не забывайте, что паять нужно на поверхности, стойкой к влиянию высоких температур! После всех работ деталь должна остыть, ни в коем случае не надо помогать ей это сделать принудительно (например, водой), пусть остывает сама по себе. В ходе данного процесса часть окалины сама отойдет от металла:
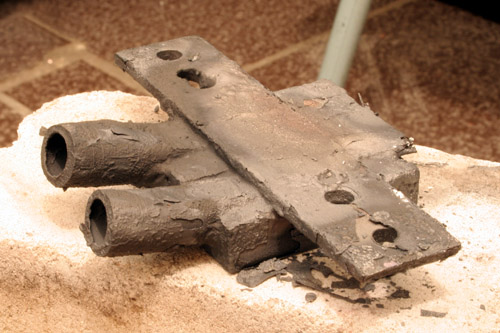
После полного остывания необходимо почистить деталь. Для начала стоит очистить всю возможную окалину щеткой, она почти везде легко отходит при малейшем прикосновении. После этого я замочил плод своих трудов в аккумуляторном электролите, который в основной массе состоит из серной кислоты и стоит около $5 за 1 литр. Пара часов – и перед нами замечательный результат. Ко всему прочему, данный способ позволит избавиться от окалины и внутри самого водоблока. Можно, конечно, отчищать поверхность путем кипячения заготовки в уксусе или Coca-Cola, но я считаю избранный способ более эффективным и надежным.
Под конец - пара взмахов мелкой наждачной бумагой, и водоблок готов к покраске, которая защитит его от окисления и придаст более «человеческий» вид (помните, что основание красить мы не будем, т.к. лишняя прослойка существенно снизит эффективность конечного продукта).
Для начала я нанес несколько слоев обычной краски из баллончика:
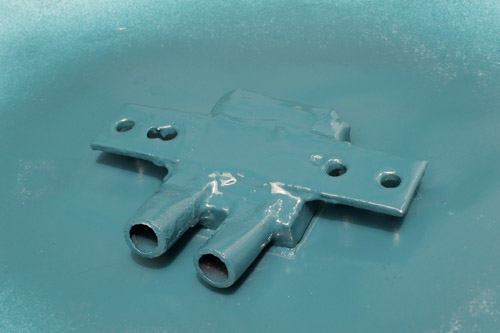
Наносить необходимо согласно инструкции, давая предыдущему слою немного подсохнуть (10-15 минут). Для предотвращения возможных подтеков, красить надо с расстояния 20-30 сантиметров.
После сушки водоблок принял практически финальный вид. Осталось навести марафет и покрасить наш теплосъемник в темно-зеленый «металик» (в стиле nVIDIA:)). Конечный его вид передать при помощи фотографии сложно, «вживую» водоблок красиво переливается и играет блёстками так:
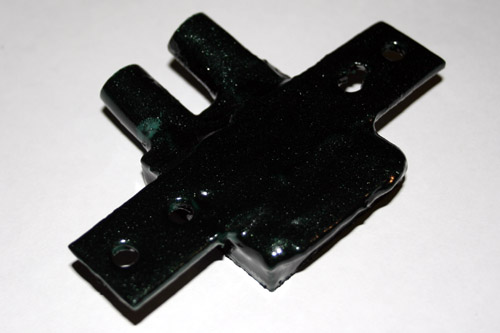
…и так:
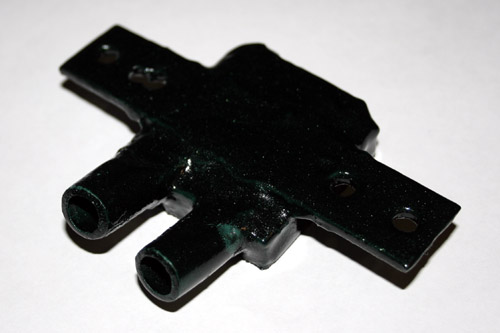
При установке проблем не возникло, к месту как раз пришлись тонкие болты для крепления водоблоков на новые видеокарты с узкими отверстиями:
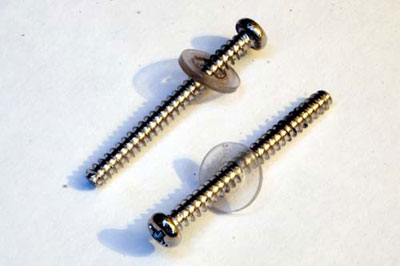
Сам чипсет раньше уже был мной «модернизирован» - мелкие конденсаторы на подложке покрыты лаком, для защиты от выпадения конденсата:
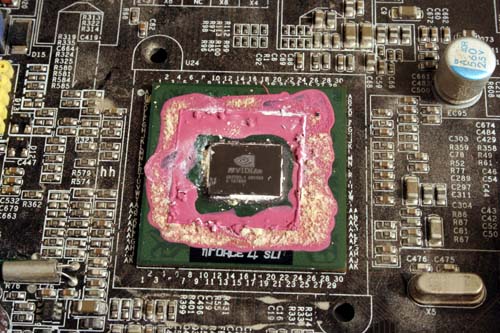
Теперь мой ПК похож на девайсы из футуристических фильмов: куча шлангов и непонятных деталей:).
Водоблок удобно расположился в отведённом для него месте:
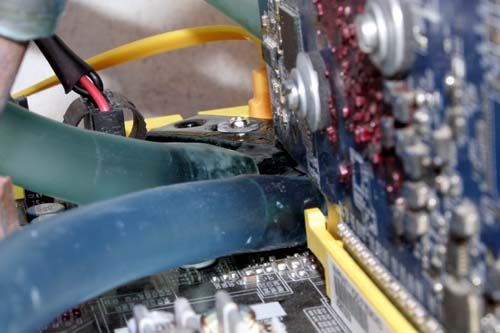
Его эффективность оказалась очень достойной: если ранее чипсет прогревался до температуры 50-55 градусов Цельсия, и при этом работа компьютера сопровождалась отчетливым воем установленного вентилятора,
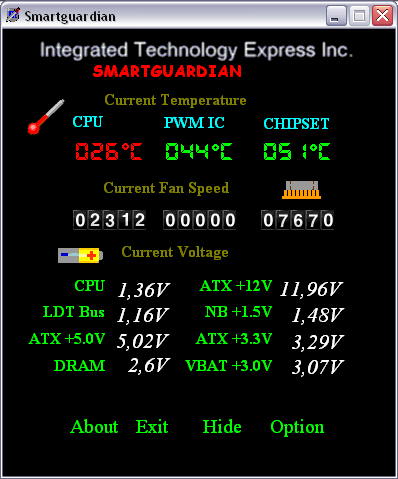
то теперь его температура на 2-3 градуса выше температуры воды в системе охлаждения:
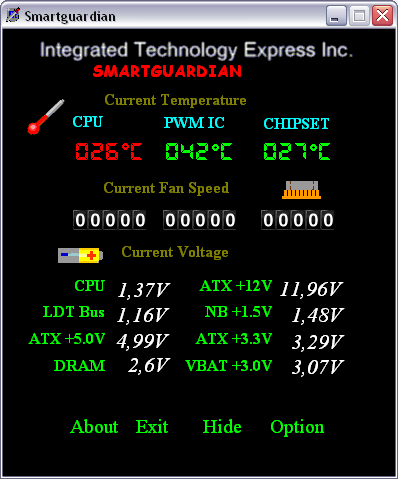
Вот таким образом, не затрачивая больших финансов и отдав приятному делу пару часов, я получил тихий, быстрый компьютер с возможностью установки данного водоблока на новую материнскую плату.
Теперь осталось избавиться от вентилятора в блоке питания, и можно будет забыть о шуме ПК во время его работы;)
Ваши пожелания и замечания по данному материалу принимаются в соответствующей ветке форума ModLabs.net.
Nota Bene: данный материал – «первая ласточка», которая публикуется на ModLabs.net благодаря «Программе передачи творческого наследия XtremeBoosters.com.ua команде ModLabs.net».
Первоисточник статьи – здесь.
Экстремальное охлаждение... Низкие и сверхнизкие температуры... Умопомрачительный разгон процессора или видеокарты.. Мировые рекорды..
Кто из оверклокеров не мечтал об этих вещах, которые когда-то были удовольствием неординарным и дорогим. Сегодня же ситуация меняется - в интернете много информации на тему самодельных систем фазового перехода, и, при наличии желания и умения создать свою, личную, пусть даже по типичной схеме, пусть не самую производительную, но намного более дешевую "фреонку" может каждый, кто действительно этого захочет. Сегодняшний материал - яркий тому пример, достойный внимания и уважения!
Структура статьи такова:
1. Введение
2. Компоненты системы
3. Сборка системы
4. Вакуумирование и заправка
5. Практическая проверка самодельной системы фазового перехода
6. Тестирование системы, анализ результатов
7. Заключение
Введение
Фреонка! Как много в этом слове (особенно для знающих людей;))!
Уже несколько лет системы фазового перехода будоражат умы оверклокеров. Это - заветная мечта любого, ведь она позволяет открыть новые, доселе неведомые горизонты разгона. Сейчас ни один новый мировой рекорд по разгону компьютерных комплектующих не обходится как минимум без применения фреонки.
Несмотря на свою долгую историю, системы охлаждения на основе фазового перехода так и не стали массовыми. Причин тому есть великое множество. Так, если говорить о самодельных вариантах, то кого-то отталкивает сложность сборки, кого-то пугает конденсат и другие сложности в процессе эксплуатации. Немаловажным сдерживающим фактором является высокая цена, ведь стоимость серийных фреонок находится у отметки «1000 у.е», что для рядового оверклокера из постсоветского пространства - немыслимые деньги за охлаждение. Самоделки же, хоть и стоят в 3-4 раза дешевле, но все равно донедавна были уделом преимущественно обеспеченных людей и истинных фанатов разгона.
В данном материале я расскажу Вам, как собрать Систему Фазового Перехода своими руками и при этом потратить сумму, эквивалентную стоимости серийной СВО.
Компоненты системы
Приступим.
Основным донором для нашей фреонки станет старый кондиционер производства Бакинского завода. Вот так он выглядит:
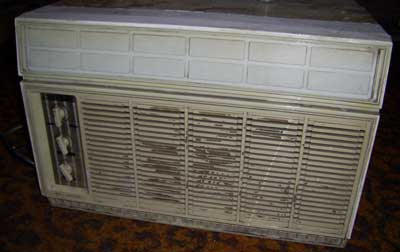
…а вот его технические характеристики:
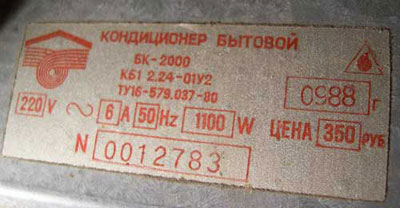
В кондиционере присутствует отдельная линия для охлаждения масла:
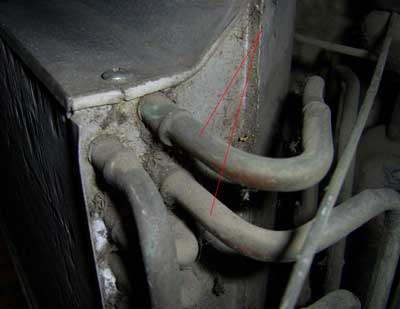
Пробный запуск показал полную работоспособность данного девайса. За несколько минут температура на испарителе опустилась до -7С:
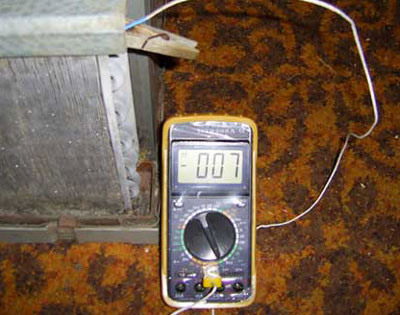
Компрессор
Модель БК-2000 использует самый производительный из используемых в данных кондиционерах компрессоров. Это - среднетемпературный роторный ХГрВ 2,2-У2 мощностью 1100 Вт +5С (В БК-1800 и ниже используют ХГрВ 1,75-У2). Для всех кондиционеров БК родным является газ R22. Охарактеризовать данный компрессор можно так:
1. Огромная потребляющая мощность, - при запуске в квартире иногда мигает свет. Так что включать данный девайс одновременно с утюгами/чайниками противопоказано.
2. Шум. Производителем заявлено 60 Дб. О спокойной работе в таких условиях можно и не мечтать
3. Ощутимый нагрев компрессора во время длительной работы. Из-за этого в нём организована отдельная ветка для охлаждения масла. Напомню, что для роторных и поршневых компрессором немного различаются температурный порог для безболезненной работы, так для поршневых компрессоров - он находится в пределах 60-70 , а для роторного - 150-160 С.
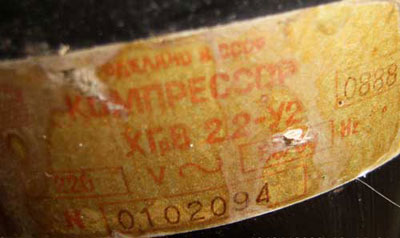
Конденсатор
Конденсатор оставляем родной, чтоб не возиться с переделыванием линии охлаждения масла. Испаритель же отрезаем, промываем и сушим (он нам еще пригодится для будущих проектов;)).
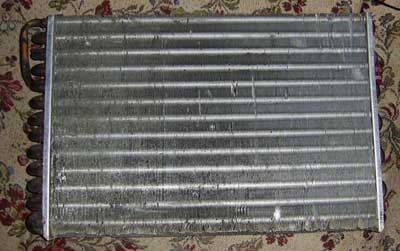
Фильтр-осушитель и клапаны Шредера
Покупаем самый большой фильтр, так как компрессор старый, и наверняка внутри него собралось много различного мусора. Так как мы берём по минимуму, то вполне можно обойтись одним клапаном Шредера для заправки и вакуумирования:
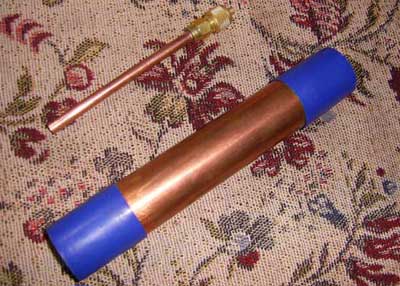
Испаритель
Он был изготовлен на заводе, из медного цилиндра диаметром 50 мм и высотой 60 мм. Имеет 4 этажа c лабиринтами, по центру просверлено отверстие диаметром 2,5 мм - для капилляра. К сожалению, меди не осталось, и штуцер пришлось изготовить из латуни:
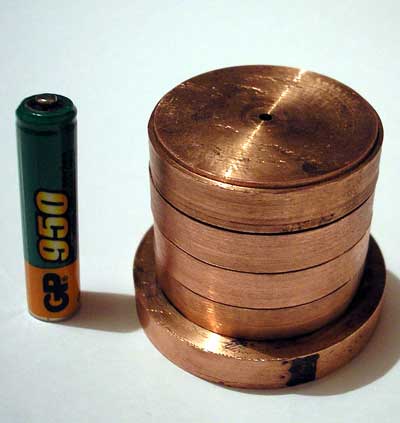
Вот он в разобранном состоянии:
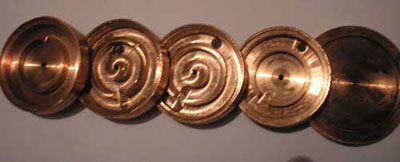
Труборез
Можно обойтись и без него, используя ножовку, но, увы, она оставляет много стружки и заусениц, которые могут забить капилляр. Да и с труборезом намного легче управляться, разрез аккуратнее и его можно использовать в труднодоступных местах. Поэтому я и купил самый дешевый труборез:
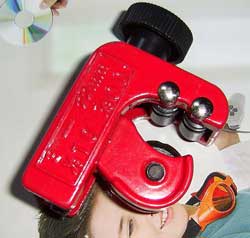
Сделаю акцент на одной его особенности: он имеет пластмассовую рукоятку, которая от постоянной нагрузки очень быстро лопается. У меня она долго не выдержала, и, как достойная альтернатива, была использована ручка от маминого агрегата для консервации
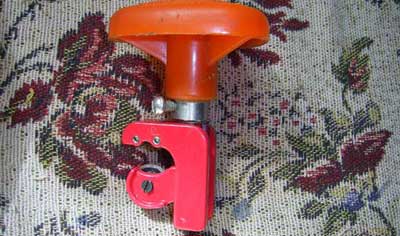
Поэтому если не хотите лишних хлопот – будьте бдительны, и покупайте труборезы только с металлическими ручками.
Капилляр
Самым распространённым и используемым является капилляр диаметром 0,7-0,8 мм, но, увы, купить его в моём городе оказалось непосильной задачей. Обойдя все магазины, торгующие холодильной техникой, я смог найти только 0,9 мм. Задача расчета длины капилляра всегда индивидуальна, обычно для этого используют таблицу Гарри Ллойда, но, увы, в ней присутствуют только капилляры с диаметром 0,7 и 0,8 мм. Обратившись со своей проблемой в ветку «Немного экстрима или фреонка своими руками - 2» на форуме overclockers.ru, я получил в своё распоряжение программу "hlad 0.3.1", с помощью которой можно рассчитать необходимую длину капилляра.
Так как в базе данных моего компрессора нет, то основные данные были введены вручную. За объем прокачиваемого газа было взято 2,2 м3/ч. При температуре конденсации 50, и температуре кипения -30 градусов длина капилляра составила 4,1 м.
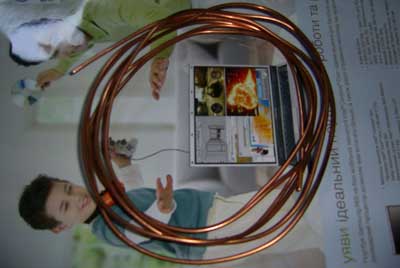
Отсасывающая трубка
Рассмотрим все возможные её вариации:
1. Медная трубка. Самый дешевый и надёжный вариант. Но есть один существенный минус - из-за плохой гибкости с ней трудно обеспечить хороший прижим испарителя к процессору.
2. Металлический заправочный шланг REFCO, идеальный вариант. Hесмотря на дороговизну, его преимущества налицо. Очень гибкий, длинный, удобный. Но найти его в продаже даже в Москве - задача весьма серьезная.
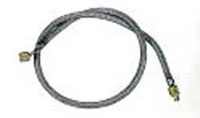
3. Желтый газовый шланг. Очень схож по свойствам с заправочным REFCO, это делает его выбором номер 2. Но имеет один существенный недостаток, - при минусовых температурах длина увеличивается на 20-30%.
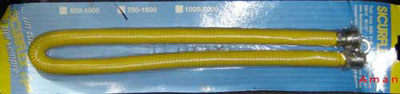
4. Медная гофрированная трубка, используется при установке кондиционеров, ею заменяют медные трубки в местах крутых изгибов, где медь попросту ломается.

Самым доступным по цене является последний вариант. Найти эту трубку можно в магазинах, которые торгуют газовым либо холодильным оборудованием.
Горелка
Это, пожалуй, самый дорогой и важный инструмент, участвующий в нашей сборке. От неё зависит качество пайки и состояние нервной системы того, кто самостоятельно делает систему фазового перехода. Исходя из финансовой стороны Вашего проекта, можно из нижеприведенного списка выбрать агрегат себе по карману.
1. МАПП газ и горелка под него. Имеет температуру горения 1300 градусов цельсия, обладает достаточной мощностью для пайки трубок. Спаять испаритель им тоже возможно, но для этого объект пайки потребуется дополнительно разогревать на плите.
Цена:
горелка – в среднем 35 у.е, баллон – 12 у.е
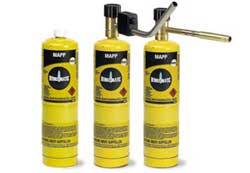
2. Турбо-пропан. Состоит из специальной горелки и пропанового баллона. Неплохой вариант, имеет достаточную температуру горения для прогрева испарителя, но если испаритель достаточно массивный, опять же придется прибегнуть к помощи плиты. Цена горелки порядка 40 у.е.
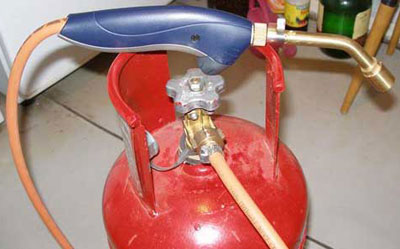
3. Пропан-кислород.
Вот этой действительно «выбор джедая». С помощью этой горелки вы сможете паять всё - от ювелирной пайки маленьких деталей и швов до тяжелых и габаритных испарителей, конденсаторов и т.д.
Здесь я решил не экономить и взять по максимуму. Осмотр цен на готовые пропано-кислородные системы поверг меня в шок, за переносную горелку с пропановым баллоном на 5 л и 1 л кислородным, требовали от 120 до 140 у.е. Единственный выход - собирать самому по деталям. На барахолке были куплены: баллон от сжатого воздуха (6 у.е) на 1 литр, и 5-тилитровый пропановый (8 у.е). Баллон для сжатого воздуха был доставлен на заправочную станцию, где его освидетельствовали, перекрасили и заправили. Горелку я купил новую, из-за мизерной разницы в цене между б/у (10 у.е) и этой (14 у.е). Новый кислородный редуктор затянул на 18 у.е, а пропановый на 4 у.е. Ну и в довесок ко всему этому пришлось взять по 2 метра шлангов. В итоге получилась вот такая горелочка, общей стоимостью 50 у.е.:
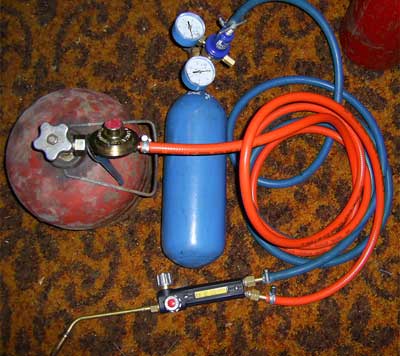
Трубки
Изначально я не знал, трубки какого именно диаметра мне понадобятся, поэтому про запас взял по метру 6 мм, 8 мм, 10 мм и 12 мм:
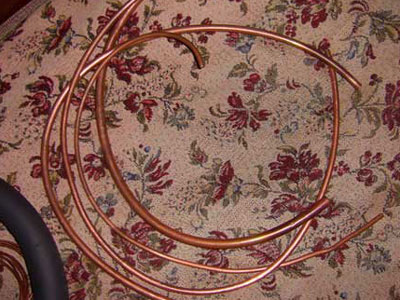
Изоляция
Трубчатая изоляция представлена в любом магазине в широком ассортименте, а вот с листовой (для изоляция материнской платы) всё намного хуже. Купить её у нас в основном можно только заранее заказав, примерно по таким расценкам: за 1 квадратный метр толщиной 10 мм просят 16 у.е., а за столько же толщиной 25 мм - 34 у.е.
Поэтому было приобретено 2 метра обычного круглого K-Flex (15 мм - внутренний, 36 мм - внешний) для изоляции трубок:
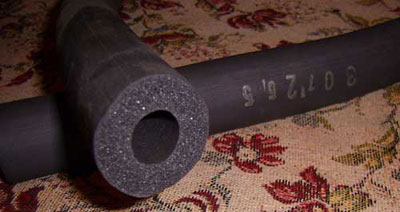
А для изоляции материнской платы я купил трубчатую, но большого диаметра (10 см), и с толщиной стенки 15 мм. Преимущество её в том, что стенки тут достаточно толстые, и при разрезе из неё получается превосходная плоская изоляция:
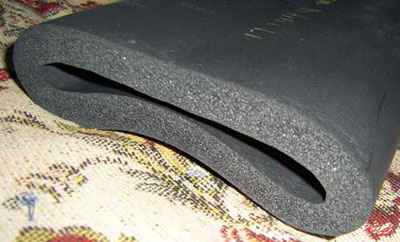
Фреон
Для заправки системы у холодильщиков был куплен один литровый баллон фреона Р-22.
Заправочный шланг, манометры
Так как манометрическую станцию я не могу себе позволить, придется ограничиться заправочным шлангом.
Припой
Все детали в системе паялись 5% Харрисом. 3-х прутков с лихвой хватит для спайки всего контура и испарителя.
Сборка системы
Сперва я решил спаять испаритель. Так как это - один из важнейших элементов системы, то качество его пайки должно быть на высоте. За несколько минут горелка разогрела испаритель докрасна, и я нежно прошёлся прутком по соединениям. Припой очень быстро и легко заполнял все стыки, расползаясь по сторонам и порывая весь испаритель.
Чтобы проверить качество пайки, нужно опрессовать испаритель. Для этого впаиваем в него клапан Шредера (предварительно не забудьте выкрутить ниппель), надуваем фреоном и опускаем в ведро с водой. С первого же раза всё спаялось удачно и течей обнаружено не было.
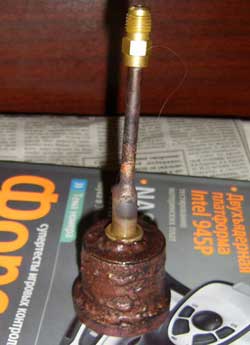
После пайки на меди образуется толстый слой окалины, и не только снаружи, но и внутри, поэтому для безотказной работы его необходимо удалить.
Сделать это можно несколькими способами:
1. Промыть испаритель в концентрированной соляной или азотной кислоте.
2. Проварить испаритель в Coca-Cola.
3. Проварить его в растворе уксусной кислоты.
Вот так выглядел мой испариетль сразу после пайки...
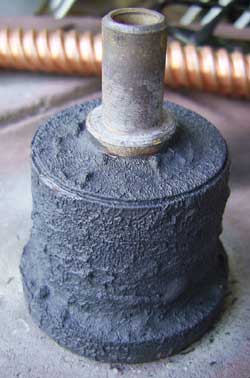
...а вот так - уже после процедуры очистки:
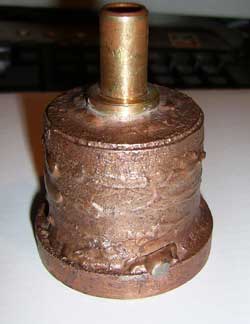
Через полчаса испаритель был чист, и я приступил к пайке отсасывающей трубки. Капилляр установился достаточно плотно, и я отрегулировал его так, чтобы он не доставал до дна 5-6 мм, и начал припаивать отсасывающую трубку. Правда, штуцер был из латуни, поэтому припой не «натекал» не него, и мне пришлось опять идти к холодильщикам, на этот раз за флюсом. С ним всё пошло как по маслу:
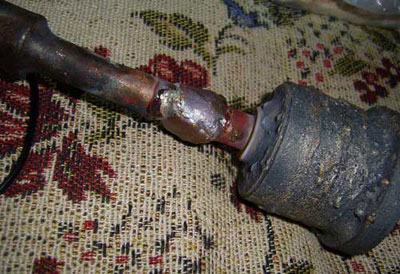
Пайка остальных деталей прошла быстро и без эксцессов.
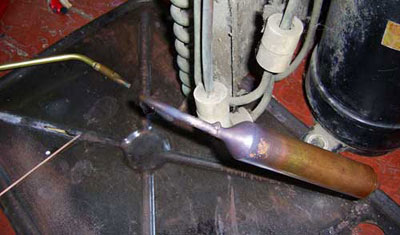
Учтите, что фильтр нужно располагать под углом, чтобы фреон лучше стекал. Когда всё уже спаяно, полезно проверить систему на течи. Для этого заправляем ее небольшим количеством фреона и промазываем всё стыки мыльным раствором. Для большей надёжности я оставил систему с фреоном на двое суток. Через указанное время было установлено, что фреон всё еще был внутри и выходил с одинаковой интенсивностью.
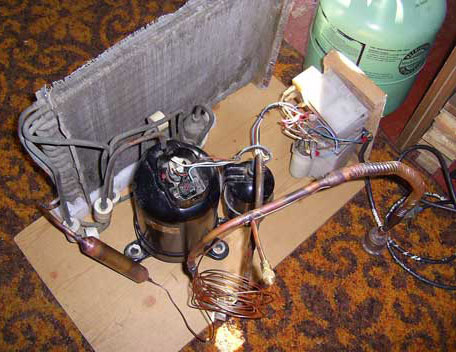
Из-за горячего нрава данного компрессора для его охлаждения я решил использовать высокооборотистые советские вентиляторы типа ВН-2 общим количеством 4 штуки:
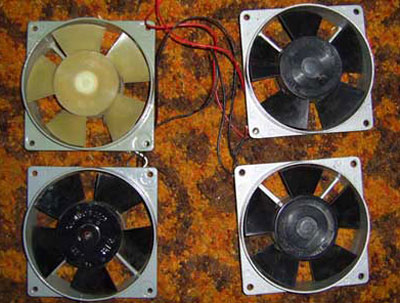
Одна пара втягивала воздух через конденсатор, другая же наоборот продувала его:
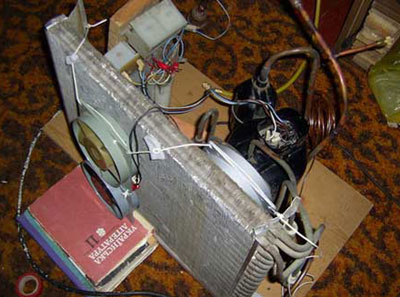
Вакуумирование и заправка
В домашних условиях самым доступным способом вакуумирования является использование в качестве вакуумного насоса старого компрессора. Но, увы, такового у меня не оказалось, поэтому я опять обратился к холодильщикам, и они с помощью вакуумного насоса REFCO за несколько минут откачали весь воздух из системы до глубокого вакуума.
Из-за большого размера конденсатора и наличия в системе ресивера, объем закачиваемого фреона достаточно велик (порядка 1 кг). В обычных фреонках этот число колеблется в переделах 300-400 грамм.
Ну что же - включаем систему, подсоединяем заправочный шланг, приоткрывая кран на баллоне на 4-6 секунд. После каждой «порции» подачи газа ждём 3-5 минут, и снова добавляем фреона. Когда испаритель начнет обмерзать, добавляем еще немного и прекращаем заправку.
Через 10-15 минут на испарителе у меня начала появляется иней, уже к 30 минуте отсасывающая трубка промерзла на 10-15 см от испарителя, а температура опустилась до «-47».
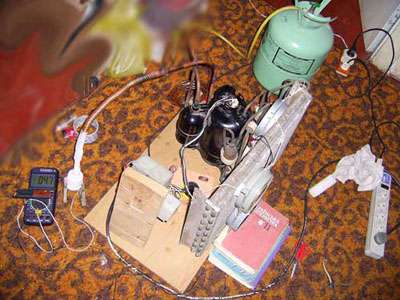
Что ж, отличный результат! Посмотрим, что будет с изоляцией. Заизолировать отсасывающую трубку особого труда не вызвало.
Включаем… и система за 15 минут выходит на -67!
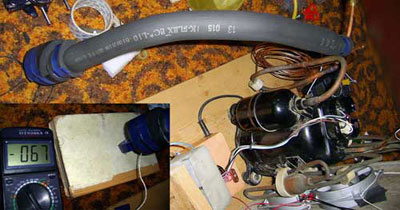
Потрясающий результат. Правда, мы должны учесть несколько факторов.
1. Для работы под нагрузкой придется добавить фреона, соответственно температура повысится.
2. Мультиметр в роли термометра далеко не лучший вариант, уже после -50 он начинает местами неплохо врать, поэтому о реальной температуре мы может только догадываться. Но сам факт достижения значения «-67» очень греет душу.
Практическая проверка самодельной системы фазового перехода
Этап подготовительный - изоляция материнской платы
К изоляции материнской платы нужно подойти со всей ответственностью, ведь даже маленькая капля конденсата может привести к нестабильности в работе, а иногда и к выходу системы из строя.
Аккуратно замеряем расположение конденсаторов и прочих элементов на плате, и вырезаем под них отверстия в изоляции (в качестве последней используем разрезанную трубчатую изоляцию, о которой говорилось выше).
Вот фото прижимной пластины из оргстекла, для плотного прилегания изоляции по всей площади контакта с материнской платой:
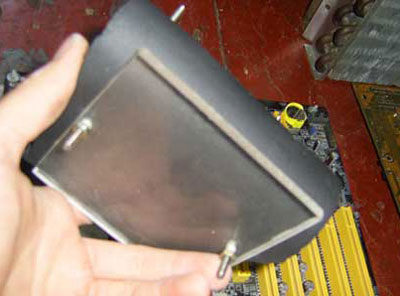
Для изоляции околосокетной зоны не использовалась никакая диэлектрическая смазка – это оказалось ненужным, ведь у меня и так получилась стабильно работающая система.
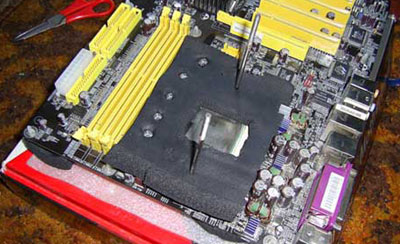
Конденсаторы тоже были заизолированы, ведь они находятся очень близко к процессорному разъему. Из-за установленного испарителя во время работы они довольно «неплохо» промерзали и покрывались инеем.
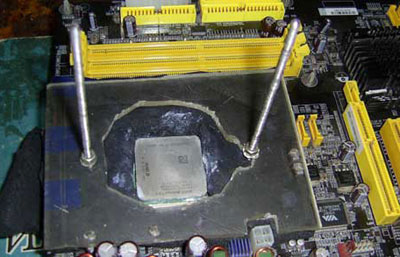
Крепление для испарителя было сделано из 15 мм фанеры, так как она, в отличие от оргстекла, спокойно держит температуры порядка -50 градусов Цельсия и ниже, тогда как 15 мм оргстекло в таких условиях промерзает насквозь.
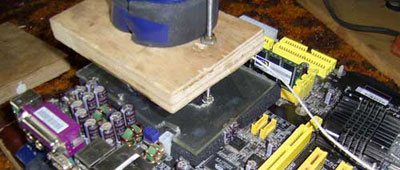
Дальнейшая проверка включенной системы показала полное отсутствие конденсата.
Испытание на железе
Из-за жесткости отсасывающей трубки было потрачено два дня на доработку крепления, так как изначально не было плотного контакта испарителя и процессора. После долгих мучений у меня всё-таки получилось обеспечить нормальный прижим испарителя к процессору.
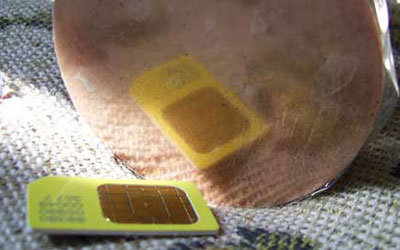
Не смотря на то, что основание испарителя отшлифовано «на коленке» с помощью пасты ГОИ и мелкой наждачной бумаги, как видите, добиться зеркального отражения довольно легко.
Для обдува околосокетной зоны и перестраховки против возникновения конденсата использовался агрессивный 120-мм вентилятор:
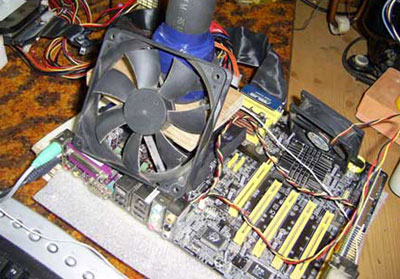
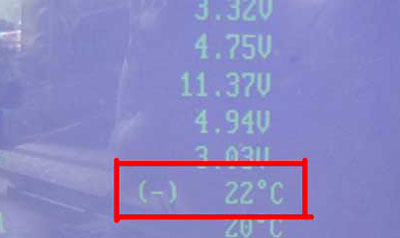
Сначала меня немного беспокоила вибрация, которая отчетливо передавалась во все стороны по полу на расстоянии 3-х метров от собранной системы, ну и, конечно, немного трясло испаритель. Правда, на стабильность это ни коим образом не повлияло, поэтому испытания проходили в режиме «чем богаты, тем и рады».
Ну что же нам делать с системой фазового перехода? Конечно, применять для разгона компонентов системы! Теперь стабильной для процессора стала частота 3050Мгц:
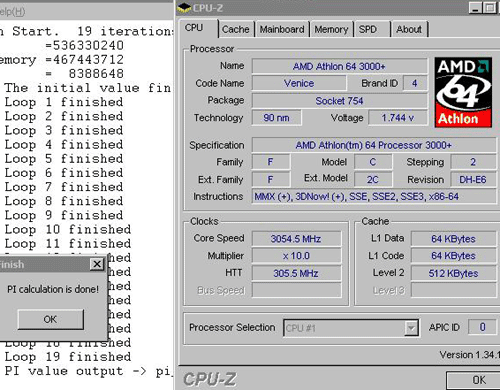
Вот так выглядела собранная система в рабочем состоянии, на фото – меряем датчиком температуру испарителя при проходе 3DMark01:
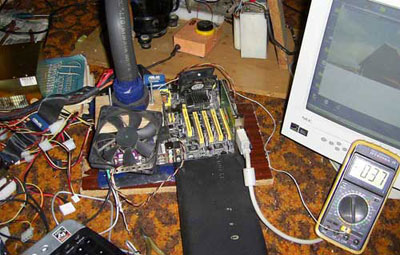
В тестах типа 3DMark01, SuperPI, SienceMark, RenderBench и так далее температура испарителя держалась в пределах -35 градусов, при более тяжелых нагрузках (типа s&m) она поднималась примерно до нуля.
Процессор попался средненький, поэтому из него получилось выжать только Russian Record (WR равен 3207Мгц). А жаль, ведь до мирового не хватило всего 29 МГц! 3178 МГц - предельная частота для моего процессора, при которой сохранялась какая-то стабильность в данных условиях:
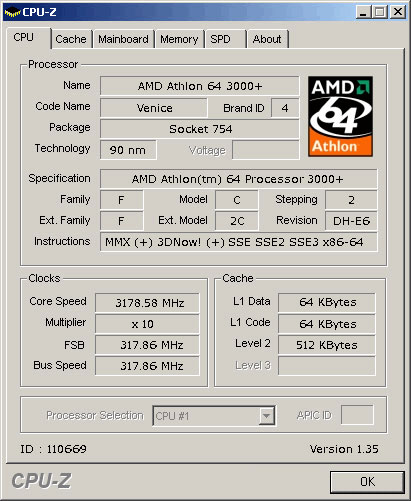
Тестирование системы, анализ результатов
Конфигурация тестового стенда:
- Процессор: АMD Athlon 64 3000+, 2.0 GHz, 1.40 V, 512 Kb (Venice, E6);
- Материнская плата: DFI LP UT nForce3 250Gb;
- Термопаста: КПТ-8;
- Система охлаждения:
Воздух: AMD Box cooler
Вода: Elite Cool «Triplex»
Фреон: custom made phase-change на базе БК-2000 - Оперативная память: 1х512 Mb DDR PC3200 TwinMos (Winbond UTT CH-5) @ 254 MHz (2-2-2-10)
- Видеокарта: GeForсe 2 MX 400
- Блок питания: Sweex Gold 650W, VSense mod 3.3V
Для «проверки боем» и оценки прироста от использования сверхнизких температур при разгоне процессора была проведена целая серия популярных тестов, по итогам которых можно судить о том, чего мы добились благодаря самодельной системе фазового перехода.
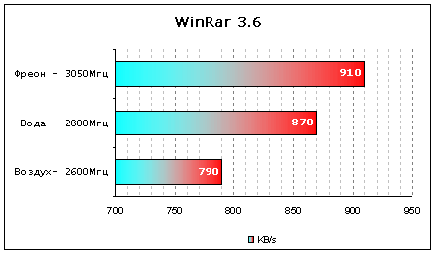
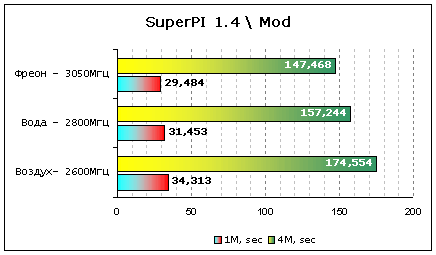
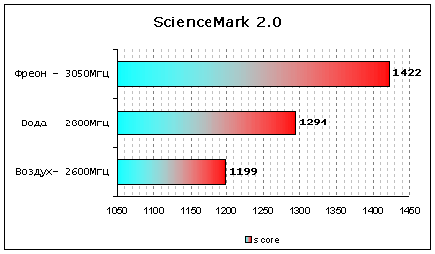
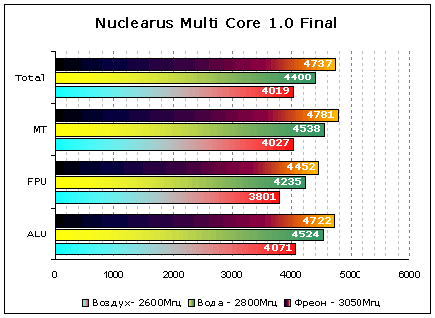
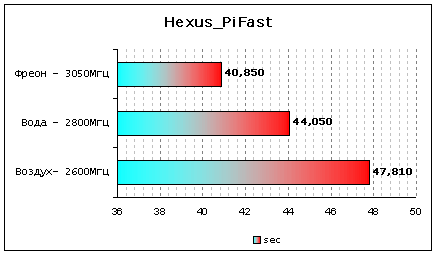
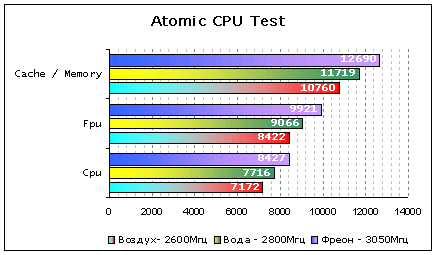
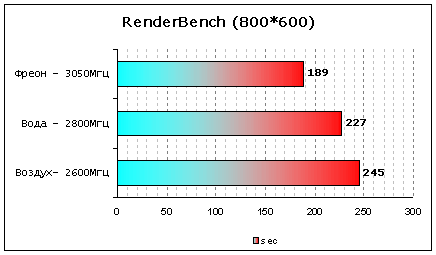
Подводя итог по тестовой части, следует отметить вполне закономерный рост производительности системы в зависимости от частоты центрального процессора, который можно изобразить с помощью линейного графика.
Может, для повседневного использования именно с этой фреонкой именно этой системы не так и много, но в бенчерских целях ничего лучше не придумаешь!
Заключение
Для начала - подведем итоги по стоимости самодельной системы фазового перехода в моем случае:
- кондиционер - 30 у.е
- фильтр - 3 у.е
- клапан Шредера - 1 у.е
- испаритель - 15 у.е
- труборез - 6 у.е
- капилляр - 8 у.е
- трубки - 8 у.е
- горелка - 50 у.е
- заправочный шланг – 8 у.е
- фреон - 6 у.е
- изоляция - 8 у.е
- припой - 3 у.е
всего: 144 у.е.
Фактически за сумму, равную стоимости хорошей покупной системы водяного охлаждения, можно получить отличный инструмент, который намного больше, нежели СВО, поможет любому оверклокеру в битве за рекорды.
Правда, есть у медали и вторая сторона.
Для комплексной оценки проведенной работы и полученного результата можно выделить следующие основные моменты:
плюсы -
- дешевизна;
- возможность получать сверхнизкие температуры на процессоре, благодаря чему достичь новых высот при разгоне;
- моральное удовлетворение от проделанной работы;)
минусы -
- огромное энергопотребление;
- большое тепловыделение (правда, зимой этот минус превратится в неплохой плюс:) );
- вибрация всей системы в целом и испарителя в частности (присутствует в конкретном случае только из-за особенностей примененного компрессора);
- слишком большой для нормальной работы шум системы.
Да, эту систему фазового перехода из-за перечисленных отрицательных черт нельзя использовать при работе за компьютером на протяжении длительного времени. Тем не менее, результатом лично я остался очень доволен - масса удовольствия от процесса работы и результата и возможность поработать на экстремальных частотах этого стоят!
Ну и не стоит забывать, что это - первый опыт в построении самодельной фреонки, который, безусловно, удался!
Дальше - будет лучше!;)
У Вас есть пожелания, критические замечания по данному материалу? Его обсуждение ведется здесь.
Вольтмоддинг референсных видеокарт GeForce 6600 GT
Рубрика: Разгон и модификацииДата: 03/09/2006 16:04:10
Введение
Данная статья изначально был изначально написана, как часть большого материала по видеокартам GeForce 7300 GT. Однако мы посчитали целесообразным выделить краткое руководство по вольтмоддингу GeForce 6600 GT в отдельную статью.В конкуренты GF 7300 GT в плане производительности записывают в основном рядовые модели GF 6600, но считаю, что разогнанным версиям больше к лицу состязаться с best buy прошлого сезона - GF 6600 GT, которая обладает высокими рабочими частотами и хорошей даже по нынешним меркам производительностью.
Напомню, что конвейерная схема у 6600 GT почти та же, что и у ее нынешних конкурентов – тоже 8 конвейеров, но 3 вершинных процессора против 4-х у GF 7300 GT.
Осмотр
Подробно обозревать видеокарту прошлого сезона мы сегодня не будем. Скажу только, что использовался графический адаптер MSI NX6600GT-TD128E, выполненный на референсном дизайне NVIDIA. За редким исключением, видеокарты на чипе GeForce 6600 GT используют именно эту разводку PCB – в отличие от более младших моделей производители проявили редкостное единодушие с точкой зрения инженеров NVIDIA на правильный дизайн данного графического адаптера. Так что данное руководство практически универсально.Выглядит карта таким образом:
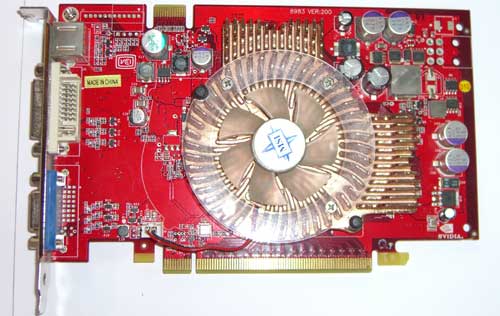
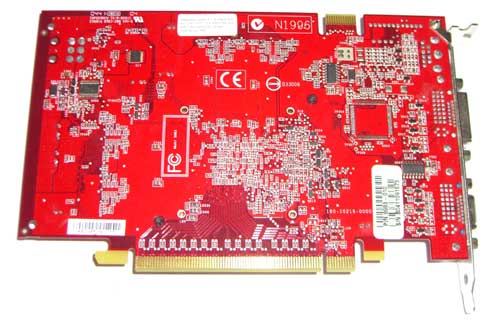
Номинальные частоты составляют 500/500 (1000) МГц, что соответствует референсным спецификациям.
На видеокарте установлена память стандарта GDDR-3 производства Samsung со временем выборки 2 нс:
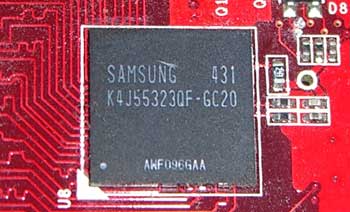
Разгон без дополнительных модификаций составил 565/625(1250) МГц, но мы на этом не остановимся.
Так сложилось, что в эпоху расцвета семейства видеокарт GF 6600 команда ModLabs.net тестировать их успевала, но вот отчитаться перед посетителями сайта о достигнутых результатах не получалось, как и выложить схему вольтмодификации. Поэтому считаю своим долгом сделать это сейчас. Как говорят, «лучше поздно, чем никогда!»
Disclaimer
В этом руководстве приведено описание изменений, успешно внесенных в конструкцию видеокарты командой ModLabs.net. Каждый из модов проверен на работоспособность и нам помог достичь желаемого результата. Однако, мы не можем обещать того, что все у всех пройдет так же удачно. Никакие претензии по поводу неработоспособности карты после модификаций не принимаются — любые проблемы означают наличие на определенном этапе вашей собственной ошибки. Ни лично автор, ни ModLabs.net не несут ответственности за любой ущерб, нанесенный повторением описанного в данном руководстве.ВНИМАНИЕ!Вольтмоддинг, если его заметят, стопроцентно отменяет всякие гарантийные обязательства. Поэтому, делать все надо максимально аккуратно, тогда есть приличный шанс, что в случае смерти карты можно будет не менее аккуратно все отпаять.
Приступать к вольтмоддингу можно только в том случае, если выполнены требования ВСЕХ нижеперечисленных пунктов:
- вы четко представляете себе, что будете делать
- вы не менее четко представляете, зачем вы это делаете
- вы умеете делать тонкую работу паяльником
- вас не пугает потеря гарантии
- вы выжали максимум из своего компьютера, но хотите большего
- все другие методы разгона видеокарты исчерпаны.
Ингредиенты
Для модификации нам понадобятся:- видеокарта GeForce 6600 GT на референсном дизайне PCB, производитель значения не имеет;
- мультиметр;
- паяльник с жалом потоньше (оптимальный вариант – 25Вт);
- подстроечные (желательно многооборотные) резисторы сопротивлением 10 кОм – 2 штуки;
- тонкие соединительные провода (желательно медные многожильные).
Модификация напряжения графического ядра (Vgpu)
Чтобы поднять напряжение на графическом чипе, необходимо понизить сопротивление резистора R37 (на моей карте подписаны не все детали):
Стандартное значение – 550 Ом, понижение сопротивления примерно на 50 Ом даст рост напряжения на 0,1 В.
Контроль напряжения осуществляется на этих конденсаторах:
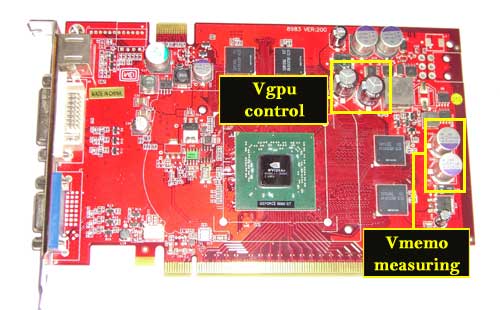
Номинальное значение для графического чипа на 6600 GT – 1,4 В. Поднятие до 1,7 В обеспечило прирост в 70 МГц – до 635 МГц.
Модификация напряжения памяти (Vmem)
Для вольтмодификации памяти на референсных GF 6600 GT необходимо снизить сопротивление указанного резистора, обозначенного на плате как R36: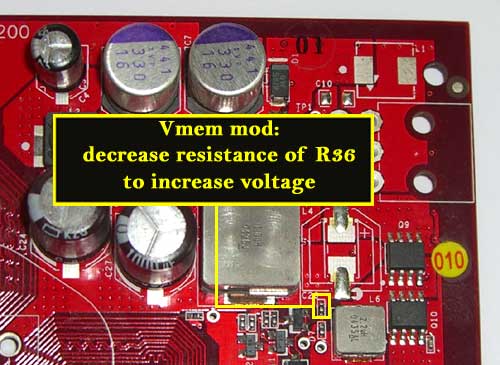
Его сопротивление составляет около 400 Ом, понижение на 10 Ом даст прибавку, равную 0,05 В.
Дефолтное напряжение Vmem на моей карте составляло 2,1 В для памяти. Повышение его до 2,2 В позволило данной карте разогнаться до 650 (1300) МГц по памяти, против 625 (1250) МГц в штатном режиме.
Тестовая конфигурация, настройки тестовых пакетов
Для проверки производительности GF 6600 GT и результатов, которых удалось добиться с помощью модификаций, был использован тот же тестовый стенд, что и в тестировании GeForce 7300 GT:- Процессор: AMD Sempron 3000+ (Palermo) Socket 939;
- Материнская плата: ASRock 939DUAL-SATA2 (Uli1695+Uli1567);
- Кулер - Arctic Cooling Alpine 64;
- Память – 2x512 MB TwinMOS (Winbond UTT CH-5, -AA4T);
- Блок питания: 600W be quiet! Dark Power ATX2.2;
- Жёсткий диск: 120Gb ATA-100 Hitachi (7200 rpm);
- Приводы: DVD-RW NEC ND-3520A
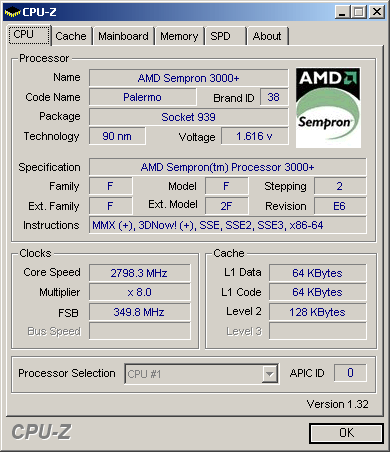
Операционная система – Windows XP SP1, для разгона графического адаптера использовалась утилита RivaTuner 2.0 RC16. Драйвера для видеокарты – ForceWare версии 91.31, соотношение качество/производительность выставлено по умолчанию и не изменялось.
Были использованы следующие тестовые пакеты:
- 3DMark 2003 v.3.6.0;
- 3DMark 2005 build 1.2.0;
- 3D Mark 2006 v.1.0.2;
- Serious Sam 2 (Direct3D) – игра версии 2.066, настройки качества изображения - "Medium", разрешение – 1024х768, использовалась демо-запись "GREENDALE";
- F.E.A.R. (Direct3D) – версия игры 1.02, настройки качества изображения - "Medium", разрешение – 1024х768, «прогонялся» стандартный демо-тест.
Производительность
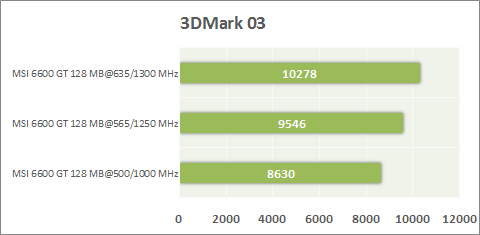
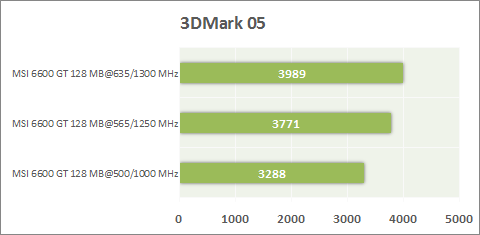
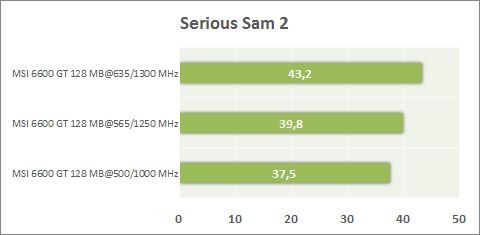
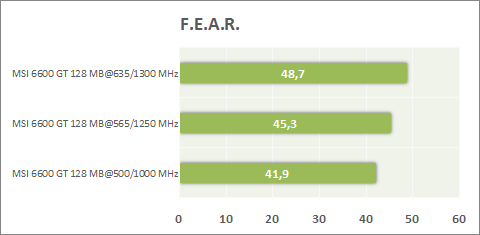
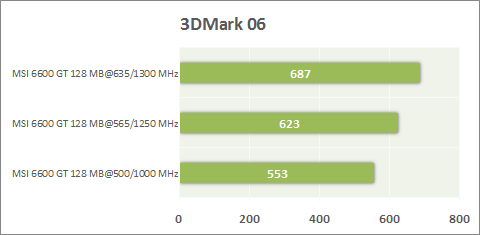